TECHNICAL EXAMINATION OF THE CLASSICAL BRONZE HORSE FROM THE METROPOLITAN MUSEUM OF ART
Kate C. Lefferts, Lawrence J. Majewski, Edward V. Sayre, Pieter Meyers, R.M. Organ , C.S. Smith , Edward V. Sayre , Robert H. Brill , I. Lynus Barnes , Thomas J. Murphy , & Frederick R. Matson
1 CONDITION AND STRUCTURE OF THE HORSE
The bronze is 40 cm high and 33.5 cm long. It weighs 11.6 kg and its overall specific gravity is 4.6. Its condition is reasonably good compared with other ancient bronzes and, in fact, it exhibits a relatively light degree of corrosion penetration. The surface has been mechanically cleaned, as indicated by scratches and file marks which interrupt the corrosion layer. There still remain, however, considerable deposits of accretions and corrosion products as described below. Observed through a binocular microscope, these are quite similar in appearance and in layered structure to those on other ancient bronzes, as confirmed by direct comparisons with ancient bronzes of unquestioned authenticity.
There are many signs of wear. The edges of the empty eye sockets, undercut and scored to hold inlays, are abraded and broken (Fig. 10). The left ear is abraded and nicked and the upper part of the right ear is missing. There are signs of wear along the edge of the mane, and the fine lines of the mane hairs are somewhat abraded. The hoof and nostrils also exhibit signs of wear. The tail is missing and the right foreleg and left rear leg are both missing below the pastern joint. The right rear leg is missing from 5 cm below the hock. There is a small rectangular indentation (4 by 5 mm and 1 mm deep) at the outside of the right fore pastern which held a repair plug. The hoof would be apt to break naturally at such a point of weakness.
Fig. 10.
The empty eye socket of the Bronze Horse once held an inlay.
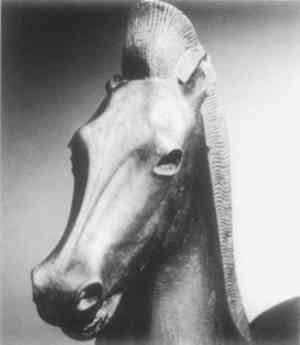 |
More than two dozen rectangular plugs are on the surface of the bronze. A few are exceptionally large, while most are small and nearly square. Five of the larger ones include two approximately 1 cm square and a rectangular one 2 by 0.8 cm on the left side of the neck and one 0.1 by 0.8 cm on each hind leg. These large plugs are not magnetic and are typical of plugs used to cover casting flaws throughout the history of casting. Most of the small square plugs are points to which a magnet is attracted. Radiographs reveal that they cover the remains of iron chaplets which supported the core within the mold during casting, which extend from the plugs into the core (Fig. 11). The presence of these chaplets is in itself convincing evidence that the horse was not cast by a sand casting technique, for chaplets such as these, which penetrate a short distance into the core but do not traverse it, would not effectively support the relatively loosely bound core used in sand casting. On the other hand, such chaplets are customary in hollow lost wax castings.
Fig. 11.
a & b. Radiographs show armature and chaplets, legs cast over an armature and the solid cast-on leg.
 |
As an integral part of the bottom of the left hoof there are three edges of a slightly raised square plate with a small square hole in the center discovered during examination (Fig. 12) This indicates that in the original casting the hoof may have been attached to a base.
Fig. 12.
Left front hoof with raised square plate and small square hole for attachment of a base.
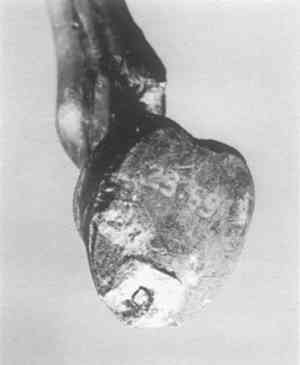 |
To obtain a section of iron armature for analysis, the plug in the left rear leg was removed as a unit by gentle tapping with needles and scalpels after hand-drilling the corners (Fig. 13). The character is similar to plugs observed by the authors on several classical bronzes. The interior surfaces are coated with black, green and orange-red corrosion products. The two long sides are bevelled, as are the sides of the hole in the horse. Under loose corrosion, the bottom of the hole is solid bronze which had been scored.
Fig. 13.
Underside of repair plug after removal from left rear leg.
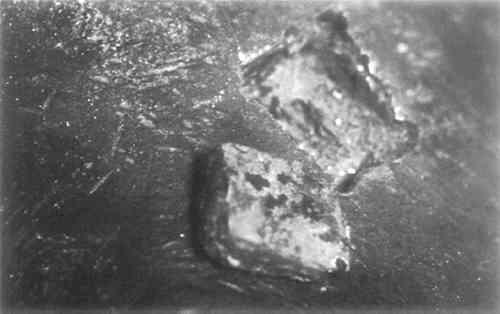 |
We drilled through the metal beneath the plug to a depth of about 19 mm. The leg is hollow without core material, and the inner surface of the bronze casting could be viewed. This inner surface is not granular as is the case with sand castings but has runs of metal similar to those observed in lost wax castings.
The internal structure of the sculpture is best revealed in the radiographs (Figs. 11a & b). Restudy of the earliest radiographs, taken in 1967 with iridium-192 radiation, shows that the armature extends through the core from the broken tail to the head, running through the length of the barrel about 20 mm down from the back, through the shoulder and up the neck. It does not run in a smooth curve, but is bent unevenly. The forehead and nose are solid bronze.
Further radiographs of the body of the horse taken at various angles with several types of radiation—high energy x-ray, cobalt-60 gamma ray, and cesium-137 gamma ray, as well as iridium-192 gamma ray—show the armature to be defined by edges of higher density. Its structure when viewed horizontally across the horse has a variable thickness of 1.5 to 2.5 mm. When viewed vertically down through the body, it is several times broader, varying quite unevenly between 10 and 15 mm. The edges of the armature are much more sharply defined when viewed from the side through its greatest thickness, as would be expected. When the support is viewed from angles oblique to its flat orientations, it is possible to observe continuous spreading of thin edge views into broader, more perpendicular views. The irregularity of the residual structure would indicate that it was originally a crude, uneven strap approximately 2 by 12 mm in cross section. Its irregularity suggests rough hand fabrication. It does not appear to be a uniform machine-made rod such as is commonly used in modern castings.
Excavation of the core material in the region of the support structure failed to produce any uncorroded iron metal. The detection of a high iron oxide concentration found in the region surrounding this structure indicates that it was indeed made of iron and that the original metal has corroded extremely.
The tapered iron chaplets run only a short distance into the core. One through the left hind quarter, 26 mm long and approximately 2 mm square, shows quite clearly on the earliest radiographs. Others can be seen at either side of the body of the horse. At the eye socket, where iron oxide was found, and in front of the throat, there are short lines of lesser density the shape of which suggests holes made by chaplets. The chaplets are capped on the surface by small bronze plugs, approximately 3mm square, which coincide with Brian Cook's chart locating magnetic points.7 One additional plug on the right cheek below the ear does not appear on his chart. The squares appearing light on the radiographs are the areas where his magnet stuck, the dark areas to which the magnet was attracted but did not stick. Probably an attempt was made to remove the chaplets before capping. The differences in density and magnetic attraction indicate the extent to which the craftsman was successful. These chaplets are not connected with the armature. As stated before, they are employed in the lost wax technique, but are not used in sand casting.
Iridium-192 radiographs of the legs show that three legs were cast solid with iron armatures, which show as darker lines running up into the core. The armature in the right hind leg leads to a surface deposit of iron oxide at its lowest extremity, confirmed by x-ray diffraction. The right foreleg is without armature and has been cast onto the body of the horse. At the join, the leg extends slightly out beyond the body. This leg would appear to have been a repair made at the time of the original casting, as its metal alloy and the corrosion products on it are similar to those of the main body of the horse. Below the join there is a semicircular hairline crack (Fig. 14). The radiograph shows that a pour of metal filled the gouged-out core for 30 or 40 mm, locking the leg to the body. The prevalence of irregularities and blow holes in the legs indicates their casting may have been a problem to the founder. The alloy (see Table I), low in lead and without zinc, has been described by foundrymen consulted as difficult to cast, as it is sluggish and does not pour easily.
Fig. 14.
Detail of join of cast on right foreleg to body.
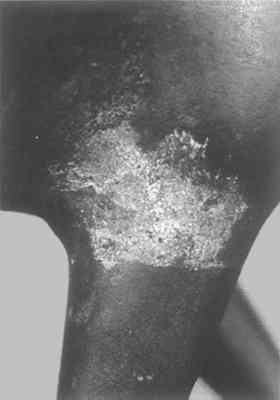 |
Table I
There is another type of repair on the left hind leg (Fig. 11b). Radiographs show that the iron armature stops just below the hock and that the lowest 35 mm of the leg is a solid casting of a denser alloy with a significantly different composition. This leg was repaired by casting on a new lower portion, using the remaining stump for attachment by including it in the mold and casting new metal over it. Radiographs indicate that this cast-on repair probably was added some time after the original fabrication of the horse because corrosion structures on the visible portions of the original leg appear to extend down into the region covered by the new casting. The angle of the hock probably shifted forward during this operation, as the horse's stride is now 20 mm longer on this side than on the right. Below the hock, covering a flaw, there is a crude fill, roughly triangular, about 12 by 15 mm, which was shown by a microchemical test to contain lead and lead carbonate.
The presence of armatures in three of the solid legs is additional conclusive evidence that the direct lost wax casting technique was employed. If the horse had been cast by either the sand casting technique or the indirect lost wax method, there would be no need for an armature in the legs as they would have been solid. However, if the artist followed the traditional direct lost wax technique and shaped the core for the body and neck, then executed the model in wax over the core, modelling the legs and tail entirely in wax, he would have needed an armature to support the wax sections during creation of the figure.
The thickness of the bronze in the body of the horse varies considerably, from 5 to 7 mm at the top of the quarters, 5 to 7 mm along the back, 7 to 8 mm along the neck, and 10 to 15 mm along the belly. There are also sudden variations at the withers and at the center of the barrel which indicate that the core was trimmed back during the modelling of shoulders and quarters. Whenever it became apparent to the sculptor during modelling that the wax walls were becoming too thin for proper casting, he would have resorted to such trimming of the underlying core.
The bronze was cast in one piece. There are no signs of rivets or welds. The metal is quite porous and the blow holes and plugged repairs show that difficulty was encountered in the casting process.
All the structural evidence indicates that the horse was cast by the lost wax casting technique, the wax having been modelled directly over a core: 1) lack of any mold marks, 2) non-uniformity of wall thickness, 3) apparent cutting back of the core, 4) use of armatures in the solid legs, 5) use of chaplets, and 6) interior runs of bronze as observed under the removed plug are all highly characteristic of the direct lost wax process.
|