AN ACCOUNT OF THE CONSERVATION AND PRESERVATION PROCEDURES FOLLOWING A FIRE AT THE HUNTINGTON LIBRARY AND ART GALLERY
Barbara Roberts , Carol Verheyen , William S. Ginell, Stanley Derelian, Leonard Krowech, Teresa Longyear, Billie Milam, Barbara Roberts, Linda Strauss, Deborah Silguero, Ron Tank, James L. Greaves, & Barbara Roberts
1 INTRODUCTIONBarbara RobertsThe following report, written by members of the conservation team who were assembled to deal with the aftermath of an electrical fire at the Huntington Gallery, Pasadena, California, of October 1985, is intended as an account of the actions that were taken for a collection in which every object was affected by residual smoke damage. There was no resident conservation staff other than for the book and paper collections.
This is a subject that is rarely made public by a museum and seldom addressed in the conservation literature (see Bibliography). Areas of specialty are addressed as follows:
- Organizing Volunteers and Supplies Following the Fire, Carol Verheyen, Preparator/Registrar, The Huntington Library
- Analytical Chemistry, William S. Ginell, Conservation Scientist, Getty Conservation Institute
- Accessioned Textiles, Stanley Derelian, Private Conservator, Santa Cruz, Ca.
- Draperies and Valances, Leonard Krowech, The Swelldom Company, Sun Valley, Ca.
- Marble Sculpture, Teresa Longyear, Private Conservator, Los Angeles, Ca.
- Bronze Sculpture, Billie Milam, Sculpture Conservator, J. Paul Getty Museum
- Furniture, Gilt Bronze Mounts, Picture Frames, Panelled Rooms, Mixed Media Objects, Barbara Roberts, Conservator of Decorative Arts and Sculpture, J. Paul Getty Museum
- Silver, Glass and Ceramics, Linda A. Strauss, Assistant Conservator of Decorative Arts, J. Paul Getty Museum
- Installation of the Collections, Deborah Silguero, Independent Mountmaker, Los Angeles, Ca.
- Books, Ron Tank, Paper Conservator, The Huntington Library
- Conclusion, Barbara Roberts
The fire originated at night in the electrical wiring of the gallery's elevator. It smoldered, presumably for some time, and ignited within the shaft. No smoke alarm was installed in the elevator shaft. Hallway sensors detected movement and set off an alarm. The only burn damage to the collections occurred when both elevator doors sprang open on the ground floor level. The resulting blast of heat destroyed the 1777 Portrait of Mrs. Edwin Lascelles by Sir Joshua Reynolds. The gilded frame was undamaged. Prior to the fire it had had a considerable buildup of surface dirt; following the blast it was extremely clean. The gilding apparently reflected the heat. An English mahogany table beneath the painting was scorched on the front rail and legs. Two tapestry covered chairs on either side of the table were scorched, and the tapestry seats were burned beyond repair.
The fire department was at the museum three minutes after receiving the alarm call. They suppressed the fire with water within 12 minutes. They were present when the elevator doors opened involuntarily. Exhaust pumps removed all excess water, and other than hot steam, there was no direct water damage. It should be noted that the local fire department conducted regular drills at the Huntington and they were extremely well prepared. They preserved the collections and the building.
The three-story elevator shaft belched smoke for approximately four minutes after the doors opened, much of which was swept upwards into the adjacent double sided stairwell. Gallery doors were not closed, and the dense smoke reached every corner of the building in minutes. It permeated the air conditioning system. A fine, blackened oily film that contained soot like contaminates was deposited anywhere the smoke could reach, including drawers inside closed desks and the interior of clock movements. (See Figures 1 and 2 for examples of the deposition of this film on the ceiling and on a marble sculpture.) Windows and doors were opened to air the building. The outside temperature and humidity levels were fairly stable.
Fig. 1.
Huntington Art Gallery—Smoke and heat damage to ceiling in hallway immediately outside elevator shaft.
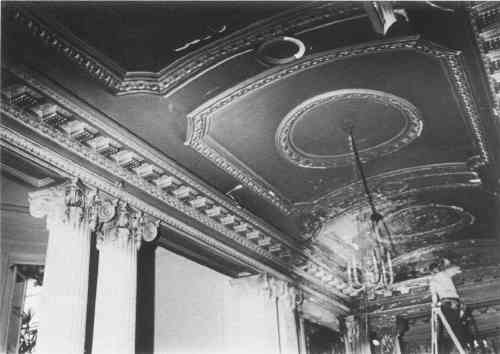 |
Fig. 2.
Cleaning test on Cleopatra by Laurent Delraux (Huntington Collection #68.10A); on table on upper floor landing.
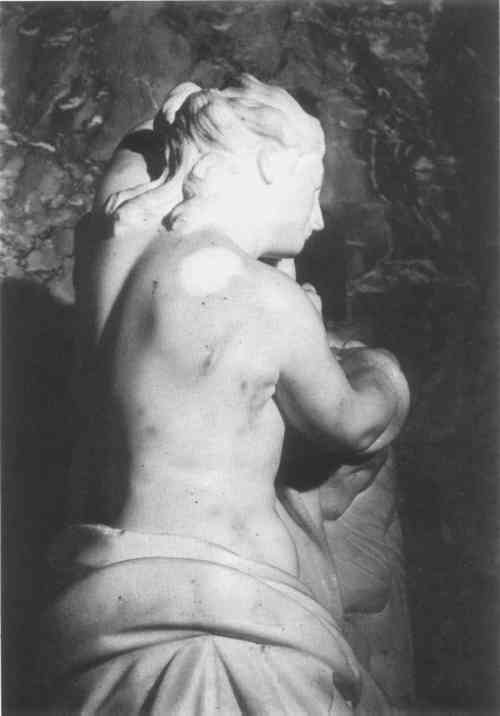 |
Initial conservation advice was to take stock of the damage and to request analysis of the oily layer to establish exactly what had to be removed. Glen Cass at the California Institute of Technology reported that the deposit was composed of approximately 50 percent black elemental carbon, mostly in the form of small black specks that would not dissolve in any solvent, and approximately 50 percent organic compounds, most containing between 24 and 36 carbon atoms and similar in structure to lubricating greases. The residue was related to wood smoke. This layer covered normal gallery dust and accumulated dirt, or previous corrosion products. It was clear that the deposits had to be removed before they dried out completely and became insoluble. This thesis was confirmed by tests conducted by the Getty Conservation Institute. Working time could be numbered in weeks rather than years. The conservators who were involved with the project were chosen for their specialties, and their contributions are documented in the following pages.
2 ORGANIZING VOLUNTEERS AND SUPPLIES FOLLOWING THE FIRECarol VerheyenFollowing the fire, the situation at the gallery was assessed by the director and the curators of the Huntington. There is no resident conservation staff for decorative arts, textiles, or paintings. They consulted with conservators from the Los Angeles County Museum of Art and the J. Paul Getty Museum, as well as scientists from the California Institute of Technology. The concensus was to proceed cautiously and without haste. The first “workday,” Octobert 26, was nine days after the fire, to clean objects in place in the gallery.
Conservators came three days after the fire to conduct tests for the removal of the sooty deposit from various types of objects. They specified which objects could be cleaned by trained volunteers, with treatments and materials written on a procedure sheet. The cleaning began with furniture, table top bronzes, and silver.
Supplies were gathered in the first week as outlined by Getty Museum conservators. Local hardware stores were important for basics such as buckets, plastic basins, garbage cans, mineral spirits, extension cords, and packing tape. A large scientific company supplied cotton swabs, absorbant cotton, dispensing bottles, Kaydry paper towels, Kimwipes, ethyl alcohol, vinyl gloves, face masks, and canned air. Second hand diapers from a diaper service were used as soft cleaning cloths, and these were periodically laundered at a dry cleaners. For emergencies, a local lab supply house was convenient for small quantities of chemicals and containers. A vacuum cleaner with a triple filter was purchased for vacuuming the upholstered furniture, tapestries, and accessioned carpets.
For some weeks, the majority of the gallery lights were not working due to the electrical damage in the elevator shaft, and the smoke smell was oppressive and liable to cause nausea on prolonged exposure. To alleviate these problems, tensor lamps and electrical fans were bought or borrowed.
For handling and storage of objects, we acquired cotton and vinyl gloves. Bed sheets were donated to cover cleaned objects. A local moving company, which moved art objects to storage during the renovation period, supplied newsprint and dozens of sturdy packing boxes of various sizes. The fragile objects (approximately 140 pieces of ceramics and glass, 400 silver objects, 16 small bronzes, five pairs of candelabra, and 12 clocks) had to be selectively wrapped in acid-free tissue paper and packed in boxes, cushioned with styrofoam “popcorn,” before being moved to the Main Gallery, which was our largest storage area.
The gallery has a photographic identification card file for each object. These were copied and the sheets were placed in the room where the objects were displayed, and moved with the object for identification purposes when boxed or covered. Conservators and volunteers alike were instructed to sign the sheet with date, treatment given, and their names. This provided an accurate record of all work carried out on an object.
Chemicals were stored in a room with outside ventilation off the basement of the gallery. A supply bucket room was established in a large bathroom off the gallery, where the volunteers were instructed to replace their buckets as they left each evening.
An appeal for help was made to the docent volunteers at the Huntington. On the first workday we had a team of 15 volunteers, four staff members, and six conservators from the J. Paul Getty Museum. The small team was necessary to keep tight control during the initial training phase. Followlng a brief orientation by Barbara Roberts and Jerry Podany from the Getty, the volunteers chose to train on a type of object with which they were most comfortable: furniture, sculpture, or silver. They received hands-on instruction in cleaning techniques from a specialist conservator. This was augmented by written handouts for each type of object, to refresh memories or to introduce new volunteers to a procedure. Initially the volunteers were asked to commit 10 to 12 hours a week to ensure continuity. Once they felt comfortable with a cleaning technique they could set their own schedule, but were asked to check in with the staff member or senior conservator working in the gallery that day. Any questions or problems were discussed with the person “on call.” This system worked well.
The delicate nature of certain objects or procedures required constant supervision by a conservator. There was a concerted effort to get most of the 113 pieces of furniture vacuumed and the wood cleaned in place in the gallery before it was moved to storage, where space was at a premium. The volunteers efficiently cleaned 130 gilt picture frames, again following a training session and a conservator's cleaning test. The frames were available in various stages, as the conservator unframed and cleaned the paintings.
It was difficult to judge the quantities of supplies that would be used,1 and the Getty Museum conservators had to fill short-term supply needs on a number of occasions. Approximately 40 volunteers worked on the collections over the course of the project, devoting close to 5,000 hours of their time.
1.Fisher Scientific Co., Tustin, Ca., was source for chemicals, cotton, gloves, masks, bottles, and “Kaydry Wipers” (paper towels) and “Kimwipes,” both manufactured by Kimberly-Clark Corp.
We learned the importance of knowing how to contact our resources, whether they be conservators, supply companies, or people to help move objects or set up work spaces. Many people were needed on a daily basis, from carpenters, construction company foremen, security guards, to custodians. Keeping communication open between all of us was important, because so much was happening every day.
Most building renovation–washing walls, painting, restoration of ceiling plasterwork, rewiring, etc.–was delayed until the majority of the art objects were in storage. Within a six week period following the fire, all art objects were moved from the galleries into three storage areas. In two of these areas, conservation treatments proceeded on the collection. The bulk of the objects were cleaned by the summer of 1986.
The last paintings and frames were cleaned by September 12, 1986, when Pinkie and The Blue Boy were re-hung in the Main Gallery. All of the paintings and furniture, and much of the sculpture and decorative arts objects were reinstalled in the gallery by the opening on September 30, 1986, 348 days after the fire.
3 ANALYTICAL CHEMISTRYWilliam S.Ginell
3.1 INVESTIGATION OF THE COMPOSITION AND AGING BEHAVIOR OF THE SOOTY DEPOSITS ON TEXTILES
The GCI investigated the need for immediate cleaning of the contaminated fabrics because of possible deleterious effects resulting from acids which could be produced by the eventual oxidation of the greasy smoke deposits.
Samples of fire-damaged contaminated linen drapery materials were extracted with an ethanol-hexane-toluene mixture and with water. Infrared spectra of the organic solvent extracts were obtained which showed that the deposits were composed primarily of soot (carbon black) particles and longchain hydrocarbons similar to waxes or greases. The water extracts of the fabric proved to be neutral.
Samples of the linen fabric were aged at elevated temperatures in air for several days to accelerate the oxidation of the smoke deposits. Infrared spectra of extracts of the aged fabric showed that a portion of the hydrocarbons were converted into compounds containing C=O, C-O, and OH functional groups. These groups are characteristic of organic acids or their precursors, however the water extracts of the aged fabrics failed to reveal the presence of water-soluble acids. Although the production rate of organic acidsat room temperature is expected to be low, it was recommended that cleaning of the contaminated textiles not be postponed any longer than necessary.
3.2 POULTICE MATERIALS FOR CARPET OR TEXTILE CLEANING
Because washing a Savonnerie carpet and an equally large Oriental silk rug was not feasible, a solvent-poultice cleaning technique was developed inconjunction with S. Derelian (see report). The poultice material used was an absorbent known as “rice husk ash”. To determine if the ash might be harmful to textiles, the composition of the material was determined by infrared, X-ray fluorescence, X-ray diffraction, and polarizing microscopial techniques. The ash was found to be composed of a glassy matrix containing mainly calcium,potassium, a very small amount of manganese, and a crystalline component identified as tridymite, a high temperature form of silica or quartz. The moistened ash was slightly alkaline which is consistent with the assumption that the glassy matrix material is a calcium potassium silicate. In view oftheir near neutrality, roundness, and ease of removal from the rug by vacuuming, it was concluded that any residual particles remaining in the rug following vacuuming would not be harmful.
Although hexane was used initially with rice husk ash in the poultice, itwas recommended that Freon 113 be employed instead because of its non-flammability, ready volatility and non-toxic properties. The efficiency of the cleaning process was followed by infrared analyses of successive poultice extracts.
3.3 ADHESIVE IDENTIFICATION
A collection of Chelsea porcelain objects that required cleaning was found to be attached to glass or wood shelf surfaces with an adhesive-saturated felt. Infrared analyses of felt samples taken from a number of locations indicated that two types of adhesive were used: A water soluble gum (possibly gum arabic or gum tragacanth) and a methanol soluble resin identified as shellac. The felt was found to be mostly wool. Identification of appropriate solvents for these adhesives allowed the porcelain objects to be removed safely from the shelves.
Analytical work was performed by Michele Derrick, Michael Schilling andWilliam Ginell, GCI; and Walter McCrone, McCrone Research Institute.
4 ACCESSIONED TEXTILESStanleyDerelianThe fire deposits settled out onto all of the textiles – one Savonnerie carpet (16′8″�23′6″), one 19th Century Persian silk carpet of approximately the same size, a small Turkish silk carpet, 122 pieces of upholstered furniture, one six-panel Savonnerie screen, and five Beauvais tapestries. The size and fragility of most of the items, combined with the nature of the smoke deposits, presented the possibility of further damage had they been handled and treated by the usually preferred aqueous immersion techniques.
Greasy soot lay on the surface of the carpets. Rolling, folding, or otherwise applying uneven pressure to the surface presented the risk of causing uneven penetration of the soot which could have left the surface streaked. Fortunately, the Savonnerie carpet had recently been cleaned and repaired, so it was capable of withstanding relatively rigorous cleaning procedures. The silk carpets, while structurally sound, were heavily soiled not only because they had been in one of the galleries with the most smoke damage, but there were prior accumulations of dirt. There was no record of cleaning other than vacuuming.
The furniture was soiled to different degrees, depending on its history and location relative to the fire. Much of the upholstery was too fragile to undergo removal, cleaning, and re-upholstering.
The tapestries, being vertically displayed, had smaller amounts of residue. For this reason, and in consideration of other problems associated with their prior history and apparently fragile nature, the decision was made to clean them with a more traditional aqueous-immersion method using Orvus. The work is being completed at the time of this writing with excellent results.
The carpets were cleaned in place. Water as a solvent was ruled out because of the hydrophobic nature of the soot, and because the silk carpet had evidence of color bleeding with water. The sheer size of the carpets made immersion in organic solvents impractical, and surface treatments with such solvents risked the possibility of carrying the contaminants deeper into the pile.
A solvent/adsorbent poultice system was considered the approach most likely to remove a significant amount of the residue with the least amount of potential additional damage. The requirements for an adsorbent were that it had to be relatively inert, not contain material that could affect fibers or dyes by pH changes or other factors, and have a physical structure that would not adhere to the fibers, leaving an unremovable residue. Most commercial organic or inorganic adsorbents were eliminated on these grounds. The material finally chosen was a commercial, inorganic, product, rice-hull ash, marketed under the name “Greasweep” (Greasweep Western, P.O. Box 28762, Sacramento, Ca 95828). (See Ginnell for an analysis of the adsorbent.)
Because of the scale of the project the usual solvent toxicity and flammability protection techniques were impractical or impossible. For this reason the solvent of choice was Freon 113 (Dupont), a solvent that is both non-flammable and relatively non-toxic.
4.1 PROCEDURE FOR APPLYING POULTICE
Approximately 10 pounds of ash was thoroughly mixed with 1-1/2 to 2 quarts of Freon 113 in a five gallon pail. Starting at one end of the carpet, one person spread the material with a shovel, and another used a “cement float” to even the mixture to a 1/4 inch depth across the width of the carpet in a band approximately 2-1/2 feet wide. A three-foot strip of polyethylene was unrolled over the poultice to retard evaporation, and allow time for adsorption onto the ash.
The polyethylene was removed after one hour. The ash was then lightly brushed with an 18-inch soft bristle floor broom to aid surface contact and speed solvent evaporation. Once evaporation was complete, the excess ash was brushed off, and an initial vacuuming removed most of that remaining. Two to four additional vacuuming passes removed the residual material.
The same basic technique was adapted for cleaning the furniture upholstery. Covering techniques using a variety of materials (paper, polyethylene, and toweling) were devised as needed to protect the wood finishes from contact with the poultice.
4.2 RESULTS
While it would have been desirable to have a quantitative measurement of cleaning effectiveness, controlled sampling of the material would have been difficult to obtain, and would have required removal of original material.
After consideration of testing methods, the recommendation of chemists from the California Institute of Technology, Pasadena, was that a simple before-and-after “wiping” test done in a systematic format would give a relative, even if subjective, visual measure of progress.
Carpets were sampled in nine representative areas by wiping with an absorbent polypropylene cloth (“Insorb,” 3-M, Product #9772). At each of the nine locations, three passes were made over the same 1-by-4-inch spot using moderate pressure. Following each treatment the same nine areas were sampled by wiping a 1-by-4-inch spot immediately adjacent to the previous one.
As mentioned, this test could give only a very subjective measure of effectiveness. Visual inspection of the cloth, and comparison to the previous sample indicated that the initial treatment removed up to 50 percent of the soot with a second treatment removing an estimated 75-90 percent of the remainder. Presumably, further treatment would remove additional soot, but it could also subject the textiles to more physical stress than was deemed acceptable.
One unresolved question is that without quantitative measurement, it is not possible to determine if the two components of the contamination (elemental carbon/hydrocarbons) were removed with the same efficiency.
4.3 SUMMARY
This procedure was devised to solve problems arising from a unique set of circumstances, and hasn't been presented as a method to be used in place of more traditional cleaning materials and techniques where those are practical and possible.
In this case a large number of large items were cleaned quickly, and furniture coverings that were too fragile to be removed and replaced were cleaned without damage. Had the smoke been of a different composition, or had there been heat or water damage, a different method might have been more appropriate.
5 DRAPERIES AND VALANCESLeonardKrowechCalled upon to work on the drapery restoration of the fine historic silk fabrics hanging in The Huntington Library, I must say we did nothing terribly different. We did not invent a process; we found no miracle chemicals. What we did was apply great care to every detail of the work, to item by item evaluation and then, working within the capabilities of a dedicated commercial firm's operation, we took the very best of our processing systems for the job. We believed the job could be done and were honored to be selected for the job.
Great care was taken to remove smoke damage and to preserve the original color, feel, texture, and hand (body) of the damask and silk passementerie. Window draperies were processed using a petroleum distillate solvent (Petroleum Naptha, flash point 106�F, closed cup, specific gravity 0.79, 6.56 pounds per gallon, consists of 63 percent naphthenes, paraffins 36 percent, 1 percent aromatic hydrocarbons) in a cleaning method developed by The Swelldom Company. Use of this type of solvent eliminates the tumbling process to reclaim the solvent; therefore, fabrics can be air dried. If properly used, this type of solvent can clean and deodorize fabrics without the loss of hand or color.
The procedures used to process the Huntington's draperies were as follows:
- To ready the draperies for processing, gauze was handsewn over the passementerie on the draperies to protect the fringe from unraveling. Hook protectors were used to protect the draperies from damage.
- The draperies were bagged individually in porous cloth bags to protect them from any mechanical action.
- All solvents re distilled to a zero fatty acid count. (Fatty acids are created when soaps and soils are combined in the dry cleaning process.) The distillation process removed all solids and impurities built up in the solvent. This was accomplished under reduced pressure.
- The solvent was charged with a 1 percent synthetic detergent to assist in the removal of all soils and smoke permeation.
- Distilled solvent was filtered through diatomacious earth many hundreds of times per minute so that cleanliness and purity could be attained and maintained.
- Clear, newly distilled solvent was readied so that the draperies could be thoroughly rinsed after cleaning.
- The draperies were bagged individually and placed in a computerized Washex lOO-pound petroleum solvent cleaning machine. The machine was geared down 50 percent from conventional dry cleaning speed so that fragile fabrics could be properly protected. Solvent was filtered through the drapery fabric for an eight hour period. The draperies were then cleaned in a very high volume of solvent to eliminate shrinkage and disintegration caused by mechanical action
- After the cleaning process, the draperies were rinsed in newly distilled solvent to remove remaining impurities.
- The draperies were lightly processed with centrifugal extraction to remove excess solvent and air dried at room temperature (72�F).
- Draperies were hand finished over tissue and stored prior to installation.
6 MARBLE SCULPTURETeresaLongyearThe conservation of sculpture after the fire included the treatment of 18 major pieces, which were primarily 18th-century portrait busts. Excluding a plaster Bust of George Frederick Handel (72.49) by Roubiliac and a terra cotta Bust of John Milton (66.11)1 by Rysbrack, all of the sculpture was of various types of fine veined, extremely white marble. Since the fire left a greasy, carbonaceous layer on every piece, cleaning and coating of the sculpture were the two principal concerns in the conservation of the collection.
Although there were no existing records concerning previous restoration or cleaning of the sculpture, they generally seemed to be in good condition. Most of the pieces did not show signs of recent cleaning or evidence of deterioration due to corrosive atmospheric elements. There were no apparent large fissures or cracks in any of the sculptures, and fortunately the fore did not come into contact with any of the pieces. However, some of the sculptures on the second floor of the Gallery were dramatically stained by dripping water due to condensation during the fire. Two extreme examples which showed the distinct drip marks caused by this sort of staining were the portraits at the top of the staircase, the Bust of Oliver Cromwell (80.19) and the Bust of John Hampden (80.18), both by Rysbrack. Beneath the layer of soot was an accumulation of grease, grime, and stains which the sculptures had acquired over years of exhibition. The types of white marble and the finishes given to the sculptures ranged from the very fine grained, highly polished, and luxurious surface of Roubiliac's Bust of Sir Peter Warren (67.53) to a more open grained, more coarsely finished surface found on the Bust of John Hampden.
When undertaking a project like the one at the Huntington it seems essential to adopt a flexible frame of mind in terms of the choice of cleaning methods. It is fundamental to note that each stone possesses its own metamorphic history and each sculpture its own history of fabrication and maintenance or neglect.
There were two key problems presented by the cleaning of the sculpture. One was the removal of the greasy, carbonaceous layer from the fire and the other was the removal of the grime and stains which lay beneath this soot layer. The primary concern was to remove the soot without creating indelible stains by driving the greasy carbon into the stone.
The loose particles of soot were initially removed with dry cotton swabs and soft bristle brushes. Washing with highly concentrated, synthetic detergents proved to be the most effective way to remove the remaining greasy, carbonaceous layer.2
On some of the sculptures the layers of grime could be cleaned by further washing with soap but most of the pieces required additional attention to even out stained surfaces.3
Gentle pouliticing was an effective method for selectively cleaning very slight surface alterations.4 Certain more obstinate stains could be easily removed with a commercial, methylene-chloride base paint stripper.5 A mild type of chemical cleaning based on the application of a gelatinous solvent containing moderately basic salts was employed for selectively cleaning perversely unyielding stains.6 Waxing of the marble after cleaning provided a protective coating and also restored an appropriate lustre to the stone.7
NOTES
1.. The cleaning of these busts involved the removal of soot with dry cotton swabs followed by cleaning with cotton swabs very slightly moistened with Stoddard Solvent.
2.. Orvus Paste, composed of sodium lauryl sulfate and diluted (20 ml to 1,000 ml distilled water) Orvus Liquid, composed of ammonium lauryl sulfate, proved to be the most effective detergents for the removal of soot. The detergents were applied with soft bristle brushes.
3.. Vulpex, a liquid soap of potassium methyl cyclohexyloleate was used for this purpose because it is an efficient degreaser and dissolves in water. A very dilute solution (5 drops to 1,000 ml distilled water) was most successful. After washing, the sculptures were rinsed with water until the rinse water was free of soap.
4.. Carboxymethylcellulose in water with a viscosity of a thick liquid such as honey, applied with a cotton swab and removed after approximately two minutes, was used for this purpose.
5.. Zyholyte, a commercial paint stripper, was used for the removal of old tape residue, paint drips, or splatters, and also some oil base stains.
6.. This solvent was a mixture of 3 percent sodium bicarbonate, 2 percent ammonium bicarbonate, 5 percent carboxymethylcellulose to 1,000 ml distilled water. For very stubborn stains 2 percent EDTA was added to the mixture. The first application of solvent lasted for approximately one to three minutes. The sculpture was then left to dry for 24 hours. (Reapplication of the mixture is possible if necessary. Regulation of the cleaning action is achieved by altering the length of time of the application. See P. Mora, L. Mora, P. Philippot, La Conservation des Peintures Murales, Bologna, 1977, p. 400-01.)
7.. After cleaning, small emergency repair of breaks or joints were made with epoxy resin (either Ablebond 342-1 or HXTAL NYL-1). No significant cosmetic work such as refilling cracks or losses was carried out. Renaissance Wax, a microcrystalline commercial wax, was used for waxing very fine surfaced sculptures. Kiwi Bois Neutre, a commercial mixture of microcrystalline and carnauba wax, was used for sculptures with more coarse, absorbent surfaces.
1 BRONZE SCULPTUREBillieMilamNumerous problems were encountered in the conservation of the bronze sculpture during the emergency period in the aftermath of the fire, as there was no conservator on staff nor enough conservators available to do all the cleaning of the sculpture. The more fragile and early bronze sculptures were cleaned by the conservator, while other pieces, having been tested, were cleaned by volunteers working under the conservator's supervision, utilizing the procedure described below.
Loose soot and surface dirt were blown off with compressed air. The surface of the bronze was then gently brushed with a soft bristle Japanese brush. Metal bristle brushes were avoided because they would scratch the surface of the sculpture. A mild solution of deionized water with ethanol and Basic H mild detergent1 or Orvis Paste2 was used to remove soot from the patina. This solution was applied with slightly dampened cotton swabs of varying sizes to small areas of the patina, repeating until the swabs were clean. Areas were then rinsed using the same technique of slightly dampened swabs, only this time with deionized water. The surface was blotted dry immediately with a soft diaper or tissue, then buffed using a completely dry tissue. Occasionally a light discoloration appeared on the buffing cloth, presumably from pigmented or discolored wax. An initial suggestion by another conservator who was not familiar with Renaissance bronzes to use ethanol as a means of removing soot was discontinued, as this could cause blanching to some coatings on these pieces.
A more complex problem arose on the life-size bronze sculpture of Diana by Houdon (27.186). This sculpture had an opaque black patina. After cleaning the surface with the previously described method, a crate was recommended to protect it during renovation and painting of the hallway in which it stood. The crate was to have been lined with a waterproof liner and the sculpture wrapped in acid free tissue and/or cotton sheets. However, due to an alteration in the original specifications, the sculpture was placed in a plywood crate coated on the interior with a polyurethane sealant. The sculpture was partially covered by a cotton sheet, leaving the lower legs and base exposed. The conservator was not present, and this discrepancy in the crate's manufacture was not brought to the attention of the conservator or curator before the crate was closed. During the six month period that the sculpture was encased, the humidity exceeded 90 percent on three occasions due to system malfunction. The crating deficiencies combined with the exceptionally high humidity resulted in an alteration of the bronze surface. The patina on the unprotected areas became sticky and viscous, and had a putrid odor. The film was similar in appearance to an organic coating swelled with solvent.
There were two possible causes. First, that a solvent retained in the polyurethane sealant eventually evaporated and was absorbed by an organic coating on the bronze. The upper part of the sculpture covered by the cloth was only slightly tacky; therefore, the solvent in gas form (that was heavier than air) preferentially attacked the unprotected lower areas. Second, that the resin coating on the bronze contained corrosion products (see analysis below). It was possible that the formaldehyde adhesive used in the production of the plywood used for the crate played a role in causing this corrosion. As formaldehyde outgasses, especially in conditions of high humidity, a hydrolysis reaction may occur which emits formaldehyde fumes, and thus metal corrosion can occur.
To obtain technical information on the composition of the surface material, two samples were sent to the Getty Conservation Institution chemical analysis.4 The sample from the uncovered area at the base of the sculpture was removed with a wooden orange stick, while the sample from the covered area was removed with an ethanol soaked swab. Infrared analysis showed that both samples were complex mixtures containing the same components. The major constituents identified from the IR spectra were wax and copper salts (copper formate and/or copper acetate, and malachite). The copper salt may have been a reaction product from volatiles emitted during the storage period. However, without knowing the composition of the patina prior to storage, it is impossible to ascertain absolutely whether the copper salts were formed during this period.
The viscous residue had to be removed from the surface of the sculpture. Several solvents were tested, the most effective being ethanol, xylene, or toluene. These were used where applicable. Swabs with distilled water were then used to remove any water soluble materials. With cleaning, the surface became less of a black-opaque patina and more of an uneven greenish-black, transparent patina, exposing numerous flaws. Corrosion products were removed by the mechanical action of the swabs and the organic solvents. In some areas of the base and lower legs, bare metal was exposed. This was inpainted with Boucour's Magna acrylics with 3 percent B-72 in toluene. The overall surface was waxed with Brown Tre-Wax5 and Butcher's (clear) wax.6 Imperfections from repairs were slightly filled with pigmented wax7 to make them somewhat less distracting.8 The cleaning exposed a somewhat “aged” patina with streaking from weathering and signs of wear, which supported the curator's contention that the damaged sticky film was an overcoating, possibly to disguise damage to the sculpture during a period of display outdoors prior to acquisition by the Huntington.
The bronzes at the Huntington Gallery are now clean, properly mounted and are maintained in a relatively stable, environmentally controlled gallery. It should be noted that prior to the fire, the Gallery had undertaken conservation treatments on some of the collection, and advice had been given on a number of topics, including improving environmental conditions, mounts for earthquake safety, and general maintenance. The fire intensified the need and the urgency for these conservation procedures.
NOTES
1.. Shackley distributor, Los Angeles.
2.. Conservation Materials, Ltd., 240 Freeport Blvd., Sparks, Nev. 89431.
3.. “Formaldehyde: A Survey of Airborne Concentrations and Sources,” Science Applications, Inc., Hermosa Beach, Calif., 25 June 1984. Carpenter, J. and Hatchfield, P., “Formaldehyde: How Great is the Danger to Museum Collections?”, Center for Conservation and Technical Studies, Harvard University Art Museums, Cambridge Mass., 1987.
4.. Getty Conservation Institute: Frank Preusser, Head of Scientific; William Ginell, Head Material Scientist; and Michelle Derrick of GCI, who ran the FTIR tests with KBr pellet.
5.. Boucour Artist Colors, Inc., Garnerville, N.Y. 10923.
6.. Rohm & Haas Acryloid B-72 available from Conservation Materials, Ltd.
7.. Trewax Co., Santa Fe Springs, Calif. 90607.
8.. Butcher Polish Co., Marlborough, Mass. 01752.
1 FURNITURE, GILT BRASS MOUNTS, PICTURE FRAMES, MIXED MEDIA OBJECTSBarbaraRobertsWith the exception of 18th-century French pieces, much of the cleaning of furniture, picture frames, and mixed media objects was carried out by volunteers whose work was supervised by the author. An example of the instructions provided is the handout sheet given to the furniture volunteers, which reads as follows.
Do not clean furniture in the Large Drawing Room and Library Room. Do not clean other pieces of furniture which are so marked by notes left on the piece. Do not clean brass/bronze mounts until trained. Before beginning work on a piece, always check record sheets in each room to see what treatment remains to be done on that piece.
- Always wear gloves when handling the furniture; change them regularly as they get dirty; throw away dirty gloves.
- Face masks are recommended although none of the solvents are very toxic; take a break outside the Gallery every hour or so; be careful around portable lights, which can easily be knocked over and cause considerable damage.
- Only one person is to work on any single piece of furniture.
- Check for any loose pieces of veneer. If loose, do not treat; note problems on record sheet in that room.
- If cleaning wood on upholstered furniture, do not touch the fabrics.
- Clean with mineral spirits (an odorless paint thinner) on a damp cotton swab; wipe off residue; keep changing the cotton; keep going over the surface until black residue is off the piece, but do not go on and on — remember you are only to be cleaning off surface dirt. Then wipe surface with diaper repeatedly; it is critical to completely dry the surface before going on.
- Ormolu (gilt brass) mounts and gilt wood are not to be cleaned until further training from Barbara Roberts.
- Note on the record sheets left in each room what you have done on a piece and what solvent you have used; sign your initials next to your entry.
- On the next day you return, go back and buff pieces you cleaned the day before to ensure there is not residual grease coming out of cracks; then cover the piece with a clean sheet.
- Before you leave the Gallery, store your bucket containing solvents etc. in the men's room; put dirty diapers, cotton, gloves, etc. in marked plastic trash cans.
- Label and identify the solvents in all bottles which are kept in your bucket. Label your bucket by writing your name on the tape placed on the outside of each bucket.
There were various hazards such as lifting veneer or mixed media surfaces, and these pieces were cleaned by the author. In general, the above procedures worked well. There was a problem with blooming, or a whitening of the wax on occasional pieces of English furniture where there was a heavy wax buildup, particularly on carved areas. Volunteers stopped using mineral spirits as soon as blooming was observed. A solution of two parts denatured alcohol, distilled white vinegar and gum turpentine with one part linseed oil was used to remove blooming by two specially trained volunteers. This mixture, (which differs from the Winterthur recipe of equal parts linseed oil, turpentine and vinegar) if applied well shaken and very sparingly on cotton swabs, buffed immediately and buffed hard again the next day, is not a problem when applied as a single application. It removes the whiteness or blooming immediately. Under no circumstances should it be used for general application or on a regular basis.1 The bloomed areas did not respond to polishing or to reforming with more wax.
The conservator used mineral spirits to remove grime from leather table tops. Gilt brass mounts on furniture were wiped off with Q-Tip swabs or cloths dampened with mineral spirits and buffed with a dry diaper in situ. At some later stage it would be advisable to remove the mounts and wash them completely. This is a time consuming operation and was considered low priority in the aftermath of the fire.
1.1 PICTURE FRAMES
All frames were checked for oil or water gilding by the author before the volunteers began work. Notes were left on the frames to be cleaned only by the author, usually those in poor condition or that bloomed during spot cleaning with mineral spirits. In general, the frames were dirty, both from the deposit and from residual dust. There were a number of flaking areas of gesso, and previous losses to the gesso.
The frames were laid on sawhorses and loose gesso was readhered with PVA white glue2 and cleaned with mineral spirits on small swabs. Teams of three or four worked on the larger frames.
1.2 CARVED PANEL ROOMS AND LIGHTING FIXTURES
These were cleaned under the direction of a conservator by The Swelldom Company,3 with approximately 7 percent Orvus4 liquid detergent in water and wiped with damp sponges in the direction of the grain. Swelldom also cleaned the chandeliers and lighting fixtures with alcohol and/or a weak ammonia solution in water.
1.3 MIXED MEDIA OBJECTS (CLOCKS, CANDELABRA, ETC.)
Clock movements were removed, disassembled, and cleaned in an ultrasonic tank. Marble bases were cleaned by Teresa Longyear with the procedures outlined for marble sculpture. The gilt brass or enamel mounts were dismantled and wiped with denatured alcohol when necessary before washing in Ivory Liquid detergent in warm water and rinsed. Exterior surfaces were wiped with denatured alcohol before drying to ensure a spot-free surface. The interior of each piece was dried completely with warm air from a hair dryer. The surfaces were buffed with a soft cloth. Copper corrosion products were removed when possible with a scalpel. The pieces were reassembled and stored with acid-free tissue in cardboard boxes.
NOTES
1. See Wolbers article listed in Bibliography.
2. Elmer's Glue, Borden, Inc., Columbus, Ohio 43215.
3. The Swelldom Company, Sun Valley, Calif.
4. Orvus Paste, Conservation Materials, Ltd., Sparks, Nev. 89341
1 SILVER, GLASS, AND CERAMICSLindaStraussA handout sheet was also prepared for the silver volunteers similar to that for the furniture volunteers. Unstable or difficult objects were cleaned by the author and all others by the volunteers. The silver was examined closely for loose parts, cracks, and breaks. Stable objects were dismantled whenever possible to prevent liquid from being entrapped inside them. Individual pieces were then washed in a mild solution of Ivory Liquid1 detergent, and warm tap water and rinsed with warm tap water. Candle wax residue was removed with xylene. (While other less toxic solvents such as naptha or Stoddard's solvent would have removed the wax as well, xylene was used because it was conveniently at hand. Very little wax residue remained in the cups, and it was easier to use the xylene from a small jar brought with the author than to send someone from the Huntington shopping for another solvent.) The clean silver was rinsed in ethanol to remove residual water from the surface, and dried with soft diapers. Compressed air and/or warm air from hair dryers was used to remove water from inaccessible areas.
Unstable objects that could not be dismantled and immersed in cleaning solutions due to surface imperfections, extreme fragility, or other problems were wiped with ethanol instead of being immersed in the detergent solution. An effort was made to keep the liquid only on the outer surface by using damp, not wet, cotton pads. It was felt that if any liquid from the pads penetrated the surface during the wiping, subsequently it would quickly volatilize and cause no damage to the object. The silver was then dried carefully with soft diapers. After cleaning, it was reassembled where necessary, wrapped in acid-free tissue paper, and placed in cardboard boxes to await reinstallation.
1.1 GLASS
The glass in the collection was washed in a mild solution of Ivory Liquid detergent with 1–2 percent ammonium hydroxide added to help emulsify the grease from the soot. The glass was rinsed with warm tap water and dried with soft diapers. The objects were wrapped in paper and placed in boxes to await reinstallation.
1.2 CERAMICS
Most of the ceramics in the collection were adhered to the glass shelves on which they stood. The adhesive had been applied earlier in this century and was of unknown composition. The Getty Conservation Institute Scientific Department was contacted to perform an analysis on a small piece of adhesive-saturated felt that had been removed from underneath an accessible area of one of the figures. It was determined that the primary adhesive was shellac (see Ginell report).
The ceramics were removed from the shelves by saturating the felt pads underneath them with methyl alcohol. The solvent was left for 10-15 minutes, and then gentle pressure was applied to the side of the ceramic to move it. In this manner, all the ceramics were removed from the shelves without damage.
Volunteers washed the less complex ceramics where a repair or restoration was not expected to be encountered. The more complex ceramics, with multiple restorations and easily damaged protrusions, were washed by conservators. The same cleaning solutions were used on the ceramics as on the glassware. The objects were dried with soft diapers or compressed air. Labels were retained in situ wherever possible. When removing them was unavoidable, they were saved for curatorial files. All marks uncovered by cleaning and removal of old felt were photographed and noted on individual treatment reports.
Minor problems occured during the treatments. A small area of overpaint on one piece of oriental ceramic was accidentally removed during the washing process. This was retouched using watercolors and Magna Bocour acrylic resin paints. Some small repairs separated during cleaning. These joins and other previously detached pieces found either inside pots or in curatorial files were adhered in the following manner: small fragments that would be difficult to clamp were adhered with Aron Alpha Type 732F cyanoacrylate adhesive.2 Larger pieces were readhered and losses were filled with Epoxy 330 resin.3 The same epoxy was used as a fill material and colored to match the clay body with dry pigments and fumed silica. No additional inpainting was used to disguise the repairs.
NOTES
1.. Proctor and Gamble, Cincinnati, Ohio 45202
2.. Toagosei Chemical Industry Co., Ltd., Tokyo, Japan
3.. Hughes Associates, Excelsior, Minn. 55331
1 INSTALLATION OF COLLECTIONS: EARTHQUAKE MITIGATION FOR ARTIFACTSDeborahSilgueroThe previous sections have provided a detailed account of the procedures developed to restore works of art which were smoke damaged in the Huntington Art Gallery fire. In addition to this restoration, the task of art conservation included, among other things, protection through mechani- cal restraints and isolation mounts, primarily the Gallery's sculpture and decorative objects.
The prevalence of earthquakes in California has long been the source of serious concern, and methods for mitigating the danger of this environment to art pieces have been developed which integrate the installations with exhibit designs. During an earthquake or tremor, the primary hazard derives from the lateral motion imparted to the base of the art piece. Depending on the frequency and displacement, it either threatens to overturn the piece or at higher frequencies, it may fracture a delicate porcelain. Shock and vibration isolation techniques and concepts have been applied to the mounting designs of sculpture exhibits at the Huntington Library. Two primary techniques are used, depending on the fragility of the piece. In all cases the restraint is designed to prevent the object from overturning.
When the sculpture is relatively strong, such as the bronze Bust of Henry E. Huntington by Paul Troubetakey, the restraint is “hard,” meant only to keep an object in place. In the second technique a “soft mount” is developed which permits a building to oscillate without imparting this motion to a delicate art piece such as fine porcelain. As each object is unique, so is the installation base designed for it. The The restraints are all designed as reversible systems to permit object removal for cleaning, repair, and/or study. Furthermore, exposed parts of the restraint fixtures are of plexiglass, which is transparent to the eye. Where necessary it is painted with Magna Bocur acrylic resin paints to blend with the wood or marble of the surroundings. Whenever possible, isolator elements are mounted internally to reduce the number and size of exposed structures. Finally, it is of utmost importance that the interface between the objects and mounting base not require procedures which risk any kind of damage to the art object.
In the sections to follow, brief examples of five designs are given to illustrate typical methods of both “hard” and “soft” type restraints.
1.1 HARD MOUNT…BRONZE BUST OF HENRY E. HUNTINGTON
Figure 3 illustrates the technique used on bronzes that are hollow without a base plate, necessitating a template of the section reproduced in 1/2-inch thick plexiglass. Centrally attached to this plate is a vertical aluminimum hollow rod which serves as a spacer and terminates in the bust's neck region. A mold was made in ethafoam of the neck's internal shape and used as the upper stabilization point. When this ethafoam is compressed vertically, it will expand radially and lock itself in the bronze's cavity through friction and radial pressure. Vertical compression is accomplished by means of a threaded rod inside the hollow aluminum rod, connected to a large steel washer above and below the ethafoam. Rotation of the screw located inside the pedestal draws the washers together much like the jaws of a vice. To install the bust one merely places it on the mount, and turns the screw inside the pedestal clockwise until the locking action is felt. Removal is simply accomplished by reversing the procedure. The ethafoam is soft enough to allow necessary vibration while locking the object in place.
Fig. 3.
View of “hard” mount from rear, showing hollow center rod topped with ethafoam and bolt assembly inside pedestal.
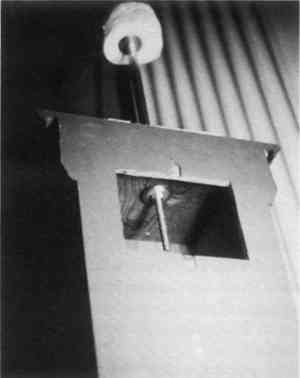 |
1.2 HARD MOUNT…MARBLE BUSTS
The installation of marble objects was significantly simpler than the bronzes, but as with the handling of all art objects, it involved some risk. The technique required that a 3/8-inch hole be drilled vertically and centrally into the base to a depth of 2-1/2 inchs (Fig. 4). In the past, this drilling task was difficult and hazardous. This project was fortunate to have had access to a drilling rig lent by the J. Paul Getty Museum. On this device, jack screws permitted accurate alignment of the drill while the art object was gently but firmly held in position. The hole was purposely bored oversized to accommodate a stainless steel restraining pin previously secured to a pedestal top. With the stainless steel pin lubricated and in place, a nominal amount of Pilacre epoxy (Philadelphia Resins Corp.) was introduced into the oversized hole. Once cured, the epoxy served as a barrier between the pin and marble, while at the same time providing a removable slip fit. For installation, one simply lowers the bust onto the pin. The slip fit restrains the object laterally in all directions but allows instant removal. It is, of course, invisible to the viewer.
Fig. 4.
View of drilled underside of figure, and base with central mounting pin. “Hard” mount.
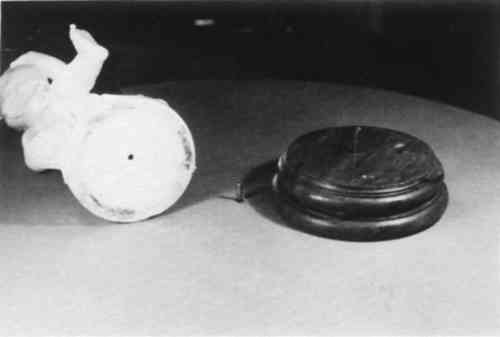 |
The foregoing technique was also used for marble objects which were resting on valuable antique surfaces. In this instance a base plate was manufactured containing the stainless steel restraining pin. A welded steel strap was fixed to the base plate and then bracketed to the rear of the display, away from public view.
1.3 HARD MOUNT…BRONZE REGENCY CANDELABRAS BY VULLIAMY
These objects are an example of a relatively sturdy artifact in which small holes may be safely drilled in the bottom of the wood insert underneath the base. This insert is matched by a 1/8;-inch thick brass plate, to which is brazed two 3-inch long threaded rods (Fig. 5). The assembly was screwed to the wooden base, then the plate was bolted to the top of the pedestal, with the rods protruding downward through the pedestal top. An access hole in the rear of the pedestal provided for installation of the nuts inside.
Fig. 5.
Base of candelabra showing wooden insert, and brass plate with threaded rods. “Hard” mount.
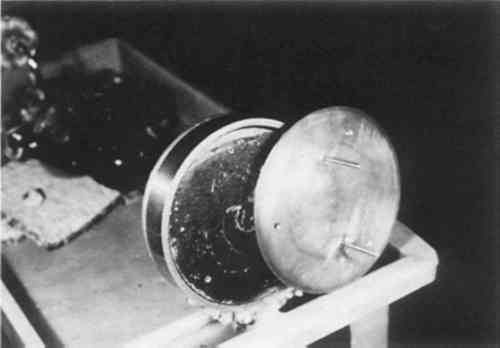 |
1.4 SOFT MOUNTS…CHELSEA PORCELAIN VASES (SHOCK AND VIBRATION ISOLATION)
Generally, in pieces of this nature where bases may be flat and where it is not possible to drill holes safely, it is necessary to fabricate a contoured fixture, against which the object is restrained. In this instance, the contour shape was prepared in 0.5-inch thick sheet acrylic which fits intimately and vertically on the backside of the porcelain (Fig. 6). Nylon-coated, 40-pound test flexible steel wire was used as a restraint noose. The stabilized mount rests on an isolation pad made of 100 percent silicone (RTV-lOO, Hastings Plastics). This system will isolate the vase from vibratory loads, and in addition direct contact with the hard plexiglass shelf is avoided. Unscrewing a small clamp releases the nylon coated wire noose, allowing the porcelain to be cleaned or studied.
Fig. 6.
“Soft mount” View including isolation pad, contoured fixture and nylon coated steel wire.
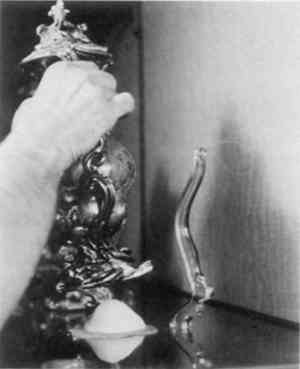 |
1.5 SOFT MOUNT…CHELSEA PORCELAIN FIGURES (EXPANSION MOUNTS)
These porcelain figures vary in shape, but usually rest on three or more contact points. Holes of approximately 3/4-inch in diameter located in the base of each object can be used to aid in mounting the object on shelves or in cases. A soft mount is inserted in the hole and the base of the mount is secured to the shelf (Fig.7). To make the mount, an aluminum foil mold the same diameter as the fabrication hole was prepared in the shape of a cylinder and filled with RTV-lOO silicone. A threaded rod, a screw, and a washer were installed inside while the silicone was wet. When the silicone cured, a nut and a washer were added to the threaded rod. The holding power is achieved by compressing the silicone by tightening the nut or screw, causing it to expand radially and bind to the inside of the porcelain figure. For visual reasons, a threaded rod of transparent plexiglass is a screwed to the 1/2-inch plexiglass shelf. Small soft silicone pads are placed beneath each point of contact with the hard shelf surface.
Fig. 7.
View of shelf with attached “soft” mount and underside of porcelain with hole for mount.
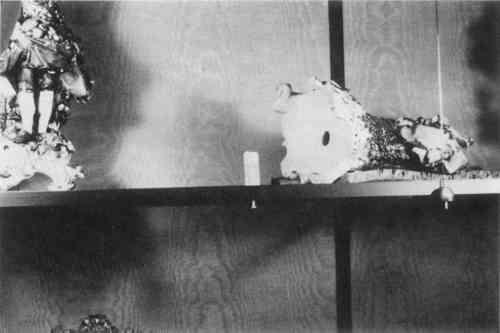 |
In closing, it must be emphasized that the foregoing protection measures are considered effective in an earthquake where the building structure remains intact. Obviously, if the earthquake is severe enough to cause ceiling structures to disintegrate, the question of artifact safety becomes academic.
2 BOOKSRonTankA matter of weeks before the fire in the Art Gallery, an expanded library facility had been opened to house 25,000 books pertaining to art history and the collections. The smoke deposits had to be removed from each volume. Most of the books had a layer of dust on top, which prevented the penetration of carbon and oily soot from damaging the books. The Art Reference Librarian with the book and paper conservation staff and a team of thirteen volunteers were divided into crews of two to a shelf area. One book at a time was removed from a shelf, held closed, and lightly vacuumed around the top, back, and bottom. A soft cloth was used to wipe the binding. Shelves were vacuumed and wiped with a mixture of five parts water and one part iso-propyl alcohol. The books were then reshelved. The entire procedure took a total of approximately 500 hours.
3 POST-FIRE TREATMENT OF OIL PAINTINGSJames L.GreavesWith the exception of the Portrait of Mrs. Edwin Lascelles (Lady Harewood) by Reynolds, which was burned beyond recovery, the oil paintings in the Huntington Art Gallery suffered no permanent physical damage. The primary problem was that of smoke/soot deposited on their surfaces. The amount varied greatly in degree depending on the location of the paintings in relationship to the circulation of smoke. (It should be noted that the smoke circulation pattern was a far more significant factor than was distance from the fire's source.)
The treatment procedures followed were relatively simple due to the general uniformity of the artwork (18th-century British and continental oil paintings on canvas) and the condition of the collection. Although a program of conservation maintenance has been initiated in recent years, the collection as a whole had hung undisturbed for at least 35 years. Ironically, past neglect of the now basic conservation practice of applying protective backings presented no problem, since the heavy dust buildup provided a removable barrier between the reverse of the stretchers and canvases and the small amount of smoke/soot which worked its way behind the paintings. (The properly backed paintings were simply wiped.)
The paint surfaces of most of the collection had very old, thick natural resin varnish coats. The appearances and solubilities suggested that some of these had wax added (traditionally, a fairly common practice in England). The combination of these layers of thick varnish and the flat brushwork characteristic of paintings of this period resulted in very smooth surfaces with virtually no impasto. This absence of surface irregularities reduced the amount of smoke/soot deposited and, together with the thick varnish layers themselves, allowed for broader cleaning methods than could have been considered for paintings of other schools.
With only minor variations the paintings were treated with the following procedure. The face of each painting was examined for insecure paint and the painting was then removed from its frame. Any debris between the stretcher and canvas was removed and the reverse of the canvas vacuumed and dry-wiped. The stretcher and tacking edges were then damp-wiped with water and/or Stoddard solvent to remove particulate dirt/debris. The smoke/soot was cleaned in front of the painting using either dilute Orvus or mixtures of Triton X100 and Triethanolamine (TEA) followed by rinses with both water and VMP naphtha or Stoddard solvent.
During cleanings some occasional blooming of the old natural resin varnishes occurred; however, with few exceptions this disappeared after rinsing with Stoddard solvent. Wax surface coatings over varnish and varnishes estimated to have some wax additives were encountered. These appeared to have softened and absorbed more smoke/soot so they were removed and thinned with appropriate solvents. The old varnishes on most paintings buffed clear; however, a few duller surfaces were given light spray coatings of Acryloid B-67 or B-72. Incidental treatment was provided for paintings exhibiting other problems such as non-fire related cleavage. A few panels were treated in a similar manner.
It should be noted that those paintings that had been restored with synthetic varnish coatings – B-67, B-72, MS2A, Ketone Resin N – over the past 10 years were as easily cleaned as those having older, harder natural resin varnishes. None of these synthetics exhibited visible retention of smoke/soot. After cleaning with aqueous solutions and rinsing with water, some of the paintings coated with synthetic varnishes either were not rinsed with solvents or odorless paint thinner was used to avoid softening those varnishes.
In physical terms of the techniques employed, much of the cleaning was done on a scale considerably broader than would normally be associated with the cleaning of easel paintings. The traditional use of swabs or wads of cotton was abandoned: the use of swabs was not warranted for reasons of safety and was logistically impractical in face of the amount of work needed; cotton wads were technically inefficient, more apt to catch on irregularities, and needlessly expensive. A general procedure was developed whereby areas of the surfaces were wiped with a sponge that was squeezed out but still relatively wet with the cleaning solution. Then the surface was immediately dried with a soft, absorbent cloth – diapers proved most effective, but Kaydry 3-ply (paper) towels also worked. This procedure was repeated until no discoloration was observed on the diaper. A clean sponge was then used to apply distilled water and dried in the same manner, repeating until traces of soap were removed. The surface was given a final wiping with VMP naphtha or Stoddard solvent applied with a cloth and dried with another. Most of the paintings, especially the large full-length portraits, were cleaned vertically. Working vertically, in itself, greatly reduced the logistical problems.
One hundred thirty-one oil paintings were cleaned, and many of these were large full-length portraits. The paintings were treated in a fraction of the time and cost which would have been required by more traditional procedures. While procedures followed might appear quite radical and are certainly not readily transferable to easel paintings done in other techniques, in this case no problems were observed and it seems unlikely that any remaining residues will present significant dangers to the paintings. However, it should be noted that many of these paintings will be more completely treated in the future and the others will be examined periodically.
4 CONCLUSIONBarbaraRobertsIn retrospect, the initial magnitude of the renovation, conservation, and cleaning problems were organized into manageable units with clear lines of communication. Volunteers were extremely observant and responded immediately if any new phenomenon was noticed. Mutual trust was established. Conservation procedures that caused problems were quickly changed, and conservators could remedy both the cause and the effects. All treatments or deviations from the norm were noted for the file.
The work was long and repetitive. Working conditions were far from good. We worked with objects in place in the Gallery, furniture on the floor, silver, porcelain, and mixed media objects in a small cloakroom with a single table – the only room with an adjacent sink, a window, and electricity.
The curators, Dr. Robert Wark and Dr. Shelly Bennett, and Preparator-Registrar Carol Verheyen were available seven days a week for questions and opinions on treatments. They painstakingly vacuumed the tapestries and seating furniture, holding the brush 1/4-inch from the surface of the textile to prevent smearing the grease. They handled conservators, volunteers, the press, insurance assessors, and many special visitors. There was unflagging activity for 11 months, including repair of the building elements by outside contractors. The plaster ceiling of the ground floor hallway was severely damaged by heat and smoke. Sections of decorative molding fell and had to be replaced.
The entire building was repainted. Wood floors were rewaxed, stained carpeting replaced, air conditioning ducting flushed, and filters constantly changed. The elevator was replaced, rewired, and a fire alarm was installed.
The Huntington was fortunate to have a “small army” of trained conservators and mountmakers within easy reach of Pasadena. To give an accurate costing on the conservation procedures is not possible, for while the building was closed, the administration took the opportunity of doing other work that had been pending for some time. It can be said that the conservation costs for the objects themselves were low in comparison to the installation and building renovation work, but had the Huntington had to import expertise or pay in full for the services of conservators, decisions and the outcome of the work would possibly have been very different. All “conservator time” was spread out over the period the gallery was closed, as we all had full-time jobs or prior commitments. Initially some Getty conservators spent two “donated” museum days a week and many weekends of their own time at the Huntington; others worked intermittent blocks of time.
This continued for about six months, slowly reducing the days as the collection was cleaned. Two people worked full-time on the mounting, with a number of added Getty staff and others at weekends to prepare large marble busts, some bronze sculpture, and particular pieces of furniture.
I personally wish to thank the J. Paul Getty Museum for releasing my colleagues and myself to work on the project, Huntington staff for their unfailing support, the volunteers for the intelligent and accurate use of conservator's advice and instructions, the conservators and mountmakers who took over their allotted specialty areas and saw their responsibilities through to opening and beyond, and to Diane Biehl for preparing this article for publication. It was an exhausting and exhilarating period; we learned a great deal. The time and effort is reflected in the gallery display. On balance, the fire, by virtue of the preservation and cleaning efforts, was beneficial to the greater part of the collections.
BIBLIOGRAPHY
Addleson, L.Materials for Building, Vol. 4: Heat and Fire and Their Effects.London: Newnes-Butterworths, 1976.
Anon. When Disaster Strikes.London: Fire Protection Association, 1986.
Anon. “Disaster Prevention/Disaster Recovery Roundup: Guide to Manufacturers and Suppliers of Products and Services for Fire, Flood, and Water Damage Control.”Technology and Conservation8 (1983): p. 37.
Barton, J.P., and Weltheiser, J.G.An Ounce of Prevention: A Handbook on Disaster Contingency Planning for Archives, Libraries and Record Centers.Toronto: Toronto Area Archivists Group Education Foundation, 1985.
Birchall, J.D.The Classification of Fire Hazards and Extinction Methods.London: Ernest Benn, 1961.
Boissonnas, A.G.“The Treatment of Fire Blistered Oil Paintings.”Studies in Conservation8 (1963): pp. 55–66.
Brown, C.“York – Up from the Ashes.”SPAB News6 (1985): pp. 6–12.
Camus. La Prevention de L'incendie dans les Constructions en Bois.Paris: Centre Technique du Bois, 1954.
Dean, G.H.York Minster Fire.1985.
Fink, E.“Stanford Flood and National Archives Fire.”Abbey Newsletter2 (1979): p. 37.
Fire Office's Committee, London. Fire Prevention and Fire Fighting in Churches.London: Fire Protection Association.
Flowers, A. and Craven, J.Disaster Plan for the Bentley Library.1976.
Fortson-Jones, J.“Practically Speaking: How to Develop a Disaster Plan for Books and Records Repositories.”History News38 (1983): pp. 30–31.
Galbreath, M.“Fire Performance Ratings.”Canadian Building Digest71 (1968).
Harper, B.“Emergency Treatment of Water-Damaged Textiles.”The Conservator3 (1979): pp. 7–8.
Jean, M. and Lucante, C.“Influence de Divers Produits de Preservation sur la Reaction au feu des Bois Proteges.” Courrier de L'industriel du Bois et de L' ameublement1974 (1974).
Kallenbach, W.et al.Brandschutz in Baudenkmaelern und Museen.Hamburg: Arbeitsgruppe Versicherung – Verband der Sachversicherer, 1980.
“Le Comportement du Bois au feu.” Cahier du Centre Technique du Bois1979 (1979): pp. 1–39.
Mackay, D.D.The Treatment of Blistered Paintings.Kingston, Canada: Queen's University, 1977.
Markman, H.“Fire Ratings of Archaic Materials and Assemblies.”Bulletin APT13 (1981): pp. 19–22.
Marty, C.“Alternativen zur Restaurierung Brandgeschadigter Gemalde.”Maltechnik-Restauro92 (1986): pp. 35–41.
Morris, J.Managing the Library Fire Risk.Berkeley: University of California, 1979.
Muchnic, S.“Restoring the Huntington: The Huntington Art Gallery Undoes the Damage from Last Fall's Near-Disastrous Fire.”Los Angeles Times Magazine (March 9, 1986): pp. 19–21.
Myers, J. N. and Bedford, D.D.Disasters: Prevention & Coping. Proceedings of the Conference, May 21-22 1980. Stanford: Stanford University, 1981.
National Fire Protection Association, Boston. Standard for the Protection of Records. Boston: National Fire Protection Association, 1975.
National Fire Protection Association, Boston. Recommended Practice for the Protection of Library Collections from Fire. Boston: National Fire Protection Association, 1975.
O'Connell, M.“Disaster Planning: Writing and Implementing Plans for Collections-Holding Institutions.”Technology and Conservation8 (1983): pp. 18–24.
Roboni, M.Al Progettazione Della Sicurezza Antincendio nel Restauro Degli Edifici.Bologna: Assircco, 1984.
Rogers, J.“The Approach to the Music Room, Brighton, Pavillon, Following Arson in 1975.”The Conservator1980 (1980): pp. 5–11.
Rohlfs, C.“Zusaetzliche Brandschutzmabnahmen Fuer Museen.”Museumkunde44 (1979): pp. 10–20.
Schmelzer, M., Baker, J.P. and Soroka, M.C.Fire and Water: Book Salavage in New York and Florence. Stroudsburg: Dowden, Hutchinson and Ross, 1978.
Schur, S.E.“Fire Protection at Mount Vernon: Incorporating Modern Fire Safety Systems into an Historic Site.”Technology and Conservation5 (1980): pp. 18–25.
Schwartzbaum, P.M.Final Iccrom Mission Report: The Conservation and Restoration of the Fire-Damaged Paintings of the Dome of the Al Aqsa Mosque, Jerusalem, 1979-83.Rome: Iccrom. 1984.
Security Letter. “How to Protect Records from Water Loss After a Fire of Damage from Burst Pipes.” Sec. Let. 12, 5 (1982): pp. 2–3.
Shorter, G.W.“Fire Endurance of Buidling Constructions.”Canadian Building Digest53 (1964).
Stocker, S.“Behandlung Verfarbter Malschichten von Brandgeschadigten Bildern des 20. Jh. durch Bestrahlung mit Leuchtstofflampen und Machtraglicher Reinigung”Maltechnik-Restauro92 (1986): pp. 42–45.
Sussman, G.Fire Prevention in Heritage BuildingBritish Columbia: Heritage Trust, 1983.
Talwar, V.V.“Care of Water and Fire Damaged Records.”Conservation of Cultural Property in India10 (1977): pp. 40–43.
Tanaka, Ichimatsu, Shimada, ShujiroKuno, Takeshi. “Damages by Fire on the Wall Paintings in the Main Hall of Horyuji Temple.”Bijutsu Kenkyu167 (1953): 53–79.
Tucker, D.M.Assessment of Fire Damaged Structures.Glasgow: Building Research Establishment, 1981.
UNESCO. “Saved from Fire and Water: Story of Rome's Book Hospital.” The UNESCO Courier. (Feb., 1957): pp. 17–19.
United Nations Organization. Guidelines for Disaster Prevention. Vol. 2: Building Measures for Minimizing the Impact of Disasters. Geneva: United Nations, 1976.
Walters, J.“A Heritage in Flames.”Historic Preservation33 (1981): pp. 10–17.
Waters, P.“Mass Treatment After a Disaster.”Conservation AdministrationEdited by Morrison, R.C., Cunha, G.M. and Tucker, N.P.North Andover, Mass.: New England Document Conservation Center, 1973.
a: Notes , References
Entire Article |