AN EPOXY/MICROBALLOON MIXTURE FOR GAP FILLING IN WOODEN OBJECTS
R. Barclay, & C. Mathias
ABSTRACT—Tensile and compressive tests were conducted on an epoxy resin/phenolic microballoons mixture in order to match its strength to test pieces of western red cedar. Heat build-up on cure of the thermosetting resin was also measured to establish recommendations for maximum thickness of fill layers. Application of the filler, including mixing, preparation of the surface, carving and inpainting, to voids in wooden objects is described. A subjective test of bond strength modifiers is described.
1 INTRODUCTION
IT IS A COMMON MISCONCEPTION that the best fill material for degraded wood is new wood, carved and finished to match. This is very rarely true as the reaction of degraded wood to fluctuations in relative humidity is different from that of new wood under similar conditions. There are both physical and chemical reasons for this. In the piece of degraded western red cedar (Thuja plicata) shown in Figure 1 (a section of a totem pole) two separate types of deterioration are present. Near the surface continual wetting and drying due to exposure to weather has created a multitude of radial checks, effectively dividing the surface into discrete zones. Below the surface brown cuboidal rot has caused the wood to lose most of its cellulose. The mechanical properties of each kind of deteriorated wood have changed. In the zoned wood, fluctuations of humidity will cause each small zone, isolated by cracks from adjacent zones, to expand and contract independently with no overall change in dimensions of the whole area. For rotted wood, cellulose, the chief component which reacts strongly to atmospheric moisture, is largely absent. The remaining material will be rather unreactive to moisture and not display normal anisotropic dimensional response. In both instances insertion of new wood could be detrimental. Dimensional changes of the new wood will impose themselves upon the original degraded material and the fill will either detach itself from the underlying wood or damage it.
Fig. 1.
Section of western red cedar totem pole showing extensive degradation. (Photo courtesy of Canadian Museum of Civilization.)
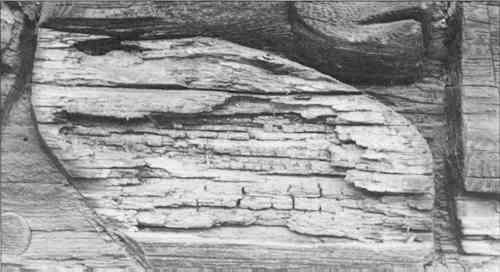 |
Wood is also less desirable for fills of the kind required in Figure 1 for two other reasons. Firstly, because of its infinite variety, it is impossible to provide a close match in grain between the new wood and the old. Thus, no matter how carefully fitted, the replacement wood will always obtrude. Secondly, and more importantly, the irregularity of losses in badly degraded wood requires removal of original material in order to ensure a good fit and provide a reasonable gluing surface. Carving a large piece of wood to match the irregularity of large, uneven voids is very difficult.
Clearly, a mouldable gap filler with physical characteristics matched to the intended application would be far superior to wood, no matter how carefully and painstakingly the work on the latter were done. It is always important to gain some insight into the condition of the wood to be filled, and to establish a clear understanding of what is required of a gap filler. The following list of criteria may be used to assess the desired qualities:
- matched to the physical characteristics of the wood
- removable (“reversible”)
- very low shrinkage
- easily applied
- easily worked
- easily inpainted
- easily available
- relatively inexpensive
- good aging characteristics
Until recently few studies had been undertaken on the physical properties of fill materials for wooden objects. Although a wide range of materials have been used by conservators for the filling of obtrusive gaps, little concern has been expressed over the long-term effect of more or less intractable substances on the surrounding wood. A recent extensive study of thirty-three traditionally used gap filling materials and several modern innovations redressed considerably this imbalance.1 The study showed that of all the gap fillers tested, filled silicone rubbers and epoxies presented the most desirable characteristics from the mechanical point of view while also having excellent handling properties. The use of both phenolic microballoons and glass bubbles for loading resins has been described previously in the conservation literature, a paper by Hatchfield2 and a book by Phillips and Selwyn3 being of particular relevance. A description of a filled silicone and its application to wooden objects has been published4 and the present paper has the same goal for the epoxy-based material.
2 MICROBALLOON-FILLED EPOXY RESIN
THE CHIEF ARGUMENTS AGAINST THE USE of epoxy resins in the filling of wooden objects are their non-reversible curing and their comparative hardness. In ideal circumstances “…the conservator shall use materials which can be removed most easily and completely.”5 Obviously, direct application of a pure epoxy resin to a wooden object results in a dramatic and irreversible change in the characteristics of the wood. However, inert fillers can be added to these resins so that the resistance to compression of the resultant material is below that of the surrounding wood and its surface adhesion to a substrate very slight. In this study Araldite AZ 3456 (with catalyst HY 3456)6 was loaded with phenolic microballoons (Union Carbide Corp. No. BJO-0930)7 to form a putty with appropriate characteristics. This epoxy resin, which has furfuryl alcohol as a solvent, was chosen for its comparatively low viscosity (1,000mPas) which permitted a very high loading of microballoons. It thus forms a very light filler which can be carved and inpainted with ease. In addition, this material presents the wood substrate with an extremely small surface area of epoxy resin, thus virtually eliminating bleeding of the resin into the wood before curing (assuming the wood has not been consolidated prior to filling). The rapid curing time of approximately three hours also reduces the likelihood of resin transfer to the wood.
The choice of phenolic microballoons requires some explanation. The authors have used both glass and phenolic microballoons for experimental fill materials and the only reason that the latter is preferred is that they appear to be more easily inpainted when working with degraded wood. This is, of course, quite subjective and depends also upon the inpainting medium chosen. The possible degradation of the phenolic resin is not a problem as the balloons are totally encapsulated in epoxy resin, and the fill itself is isolated from the substrate.
3 MECHANICAL TESTS
TESTS UNDER BOTH COMPRESSION AND TENSION were conducted on various mixtures of the microballoons and epoxy resin in order to establish a mixing ratio which gave a workable fill material with a strength below that of wood. Clearly, the strength of the wood is a factor which will vary depending upon the artifact in question. For this study the fill material was compared to fresh, kiln-dried western red cedar because this is a weak wood, with a low modulus of compression and low strength across the grain, and thus serves as a good model for deteriorated woods.
3.1 Compression Tests
Four ratios of epoxy resin to microballoons were chosen: 0.5 to 1, 1 to 1, 1.5 to 1 and 2 to 1 by weight. One centimeter cubes of these ratios were cast in a mold and allowed to cure for at least three days before testing (Figure 2). Ten cubes of each ratio were subjected to compression in an Instron compression and tensile testing instrument (Model TM, with 500kg load cell) with a cross head speed of 50mm/min. A set of similar blocks of western red cedar was subjected to the same test to afford a comparison. This test had been established previously in the absence of a comparable standard test for this purpose.8 Thus, the results are internally consistent only.
Fig. 2.
Test blocks of epoxy/microballoon filler and the mold in which they were cast.
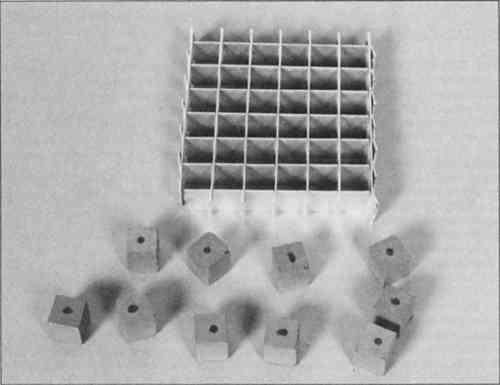 |
Figure 3 shows the point of failure of each of the ratios compared to that of cedar. Point of failure was determined as the point where irreversible compression or breakage took place. The stress/strain curve deviated from the linear at this point. For cedar, failure is sudden and dramatic, as shown in Figure 4a. The epoxy/microballoons mixture, on the other hand, exhibits the gradual change seen in Figure 4b, so that a true point of failure must be extrapolated from the portions of the curve before and after the change. From these data it can be seen that the 0.5 to 1 and the 1 to 1 mixtures have a compressive strength below that of the wood (16.2kg/cm2 and 29.9kg/cm2 respectively).
Fig. 3.
Point of failure of epoxy/microballoon test pieces and samples of western red cedar. Each plot represents 10 readings.
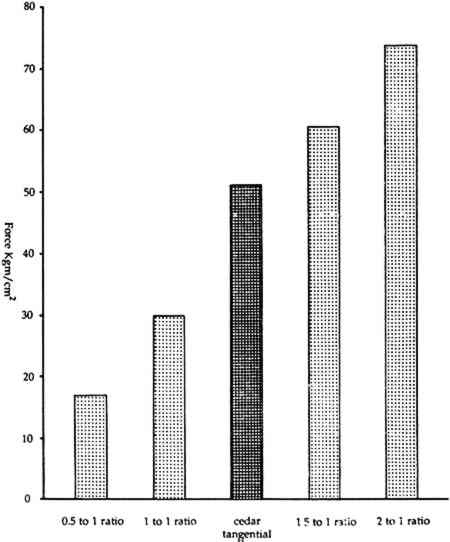 |
Fig. 4.
Characteristic stress/strain curves for a) western red cedar and b) epoxy/microballoon test sample.
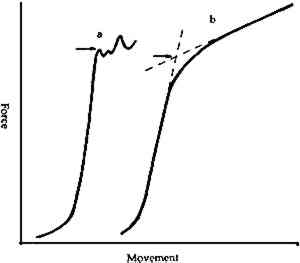 |
3.2 Tensile Tests
In cases where it is desirable to attach the fill firmly to the sides of the void it must be ensured that the fill is weaker under tension that the wood surrounding it. Shrinkage of the artifact will result in failure of the fill, not the wood. In this set of tests 1cm blocks of the same ratios of filler as the compression tests were cast between pieces of cedar so that the grain lay horizontal to the fill (Figure 5). In this orientation the test piece models the behaviour of an actual fill under tension. Before application of the filler the wood was first coated with the liquid epoxy resin to provide a sound bond between fill and wood. Although this procedure does not necessarily follow that actually used in filling a void in an artifact., it was obviously necessary in testing the filler under tension to ensure a good bond between it and the wood. When applying the filler to an artifact good adhesion may not be necessary. The test pieces were subjected to tensile stress in the Instron tester at a cross head speed of 50mm/min as above, and the site of failure noted. Site of failure was considered a more important indicator than the actual tensile strength required to break the sample, although the latter was recorded. Samples either failed within the wood, within the fill, or at the boundary of the two. The site of failure of the tests pieces is shown in Figure 6. These results indicate that failure of the weaker mixtures occurs in the majority of cases, either at the wood/fill interface or within the fill. Only in the 2 to 1 mixture was failure within the wood observed.
Fig. 5.
Tensile test samples showing the epoxy/microballoon mixture inserted between sticks of western red cedar.
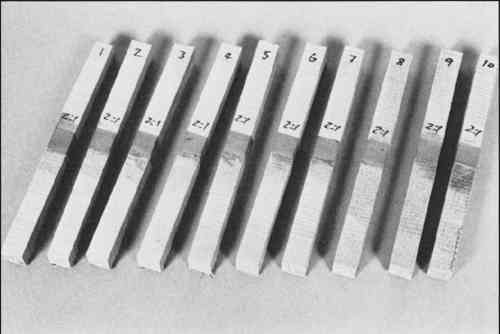 |
Fig. 6.
Site of failure under tension of epoxy/microballoon samples.
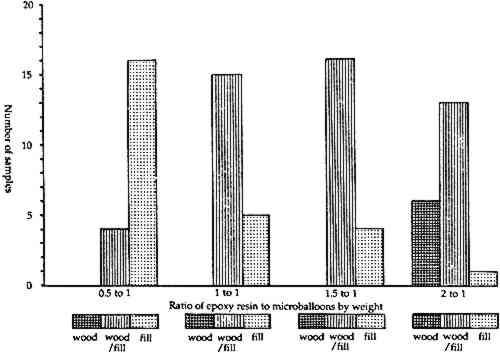 |
3.3 Mixing
Mixing a 1 to 1 ratio by weight of the filler poses problems as the volume of the microballoons is about fifty times greater than that of the resin. It is best to pre-weigh the microballoons into a sealable plastic bag and to add the mixed resin into a well in the centre. If the resin contacts the walls of the bag it tends to be less easy to mix it with the microballoons. The bag is then sealed and the mixture kneaded until thoroughly mixed. The putty has a usable life of between 15 and 30 minutes.
4 EXOTHERMIC REACTION DURING CURE
LIKE ALL THERMOSETTING RESINS, the cure of this epoxy formulation is exothermic. Also, the addition of large quantities of microballoons which are effective insulators tends to prevent rapid heat dissipation on cure. In earlier experiments it was noted that deep fills had a tendency to become dangerously hot. Tests were therefore carried out on blocks of filler to assess this problem. Two boxes 40mm3 and 80mm3 were constructed from 3/4″ (18mm) plywood to simulate voids in a wooden object. A mixture of the 1 to 1 ratio epoxy resin and microballoons was inserted and the temperature rise during cure measured with thermocouples. The cube with 40mm sides experienced a rise of 11�C (from 20�C to 31�C). The temperature in the centre of the 80mm cube rose from 20�C to 88�C in 28 minutes. These figures clearly indicate that a limit should be set on the thickness of fill material applied to an artifact. In practice it is wise to insert an underfill of an inert substance, such as polyethylene foam, so that the fill material occupies only the top portion. This is not only mechanically sound, but also economical. A maximum thickness of 20mm of epoxy/ microballoon filler would be adequate, even for large fills on such objects as totem poles, and at this thickness little or no heat build-up on cure would be expected.
5 APPLICATION
5.1 Adhesion of Fill to Wood
WHILE VERY LITTLE BLEEDING of uncured resin into the wood is expected, a barrier or resist material can be applied prior to insertion of the fill, assuming, of course, that the wood previously required no consolidation, and thus has no protective barrier already. It is clear from tests on several artifacts that no bond between the fill and the wood is actually required; in an uneven void the cured fill will lock in place physically. In shallow areas it may be necessary to increase adhesion to the wood by application of a layer of fluid epoxy resin prior to insertion of the fill. This should only be done where necessary as it will make the fill difficult to remove and cause damage to the artifact. However, the strength of bonding may be modified by application of layers of other materials. In the following set of tests the fill material was applied to wood samples coated with seven potential bond strength modifiers. Their ease of removal after curing was assessed by attempting to carve them away from the wood with a chisel. They are listed from the most easily removed, which showed almost no adhesion, to the most difficult to remove, where the wood substrate was damaged in the attempt.
- Renaissance Wax
- Klucel 2% in 1:1 ethanol/water
- Polyvinyl acetate AYAF 10% in ethanol
- Wheat starch paste 10%
- Ethulose 400 2.5% in 1:2 ethanol/water
- Acryloid B-72 10% in ethanol
- Araldite AZ-3456
It is apparent that the weaker of these materials will also serve as a resist layer to prevent penetration of the resin into the wood, should this be required. This was a subjective test applied to assess bond strength for a specific application. The results should therefore be treated with caution. Wherever possible the authors prefer to rely upon a mechanical bond, inserting thin wood dowels into existing fine cracks to assist locking if feasible.
5.2 Filling and Finishing
Voids should always be over-filled as subsequent layers of the epoxy/microballoon filler do not adhere well. The 1 to 1 ratio and more dense mixtures are easily shaped using woodworker's carving tools. It is difficult to describe the carving characteristics of the fill material except to say that it carves crisply and sharply and is capable of holding very fine detail. When being carved it reminds one of the consistency of very cold ice cream. The weaker 0.5 to 1 mixture has a tendency to crumble when being carved. Should a fill of this weakness be required, it can best be applied to large areas with no fine surface detail. Inpainting can be done with most media, but if phenolic microballoons have been used their reddish colour makes an opaque medium such as water-based acrylics desirable. If a transparent inpaint is required, glass microballoons, which yield a white filler, may be substituted. However, the brightness of the filler may still dictate use of an opaque inpainting medium. A rebuilt mortise in the lintel of a monumental wood sculpture is shown in Figure 7.Figures 8 and 9 show the surface reconstruction of a totem pole.
Fig. 7.
Rebuilt socket in the lintel of a monumental wooden object. (Photo courtesy of Canadian Museum of Civilization.)
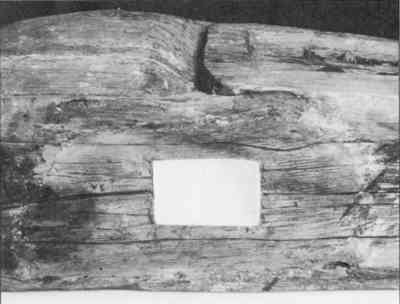 |
Fig. 8.
Totem pole detail before treatment. (Photo courtesy of Canadian Museum of Civilization.)
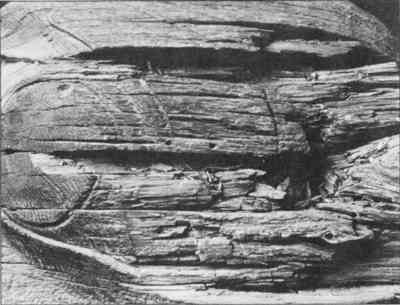 |
Fig. 9.
Totem pole detail after filling and inpainting. (Photo courtesy of Canadian Museum of Civilization.)
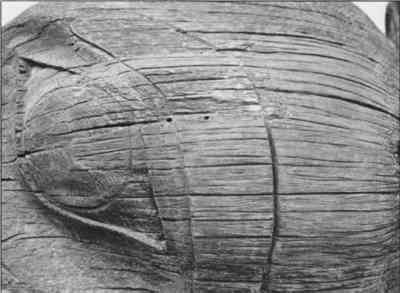 |
6 CONCLUSION
EPOXY RESINS HAVE NOT FOUND FAVOUR in conservation due to their potential for inflicting damage on surfaces to which they are applied, and also to their non-removability once cured. The application described above circumvents these two issues by treating the fill as an essentially separate unit, not bonded physically to the wood. Provided that suitable precautions are taken in its application, this fill material surpasses many in current use.
The filler described here is best suited to applications in which movement of the wood due to fluctuations in humidity is considered minimal, such as the weathered wooden structure illustrated in Figure 1. However, due to its low compressibility, it can also be used for filling cracks in sounder and more reactive wood. It should be remembered that the tests described above use only sound western red cedar because this is a weak wood, with a low modulus of compression and low strength across the grain, and thus serves as a good model for deteriorated woods. Clearly, the compressibility of other woods will differ and appropriate tests should be conducted as necessary.
ACKNOWLEDGEMENTS
THE AUTHORS WOULD LIKE TO ACKNOWLEDGE the valuable input and advice of Dr. David Grattan at all stages of this section of the research on fill materials for wood. We would also like to thank Sue Maltby for her trial work with the fill material on totem poles and for her tests of potential release materials. We are indebted to the Canadian Museum of Civilization for permission to publish the photographs of treated objects.
REFERENCES
Grattan, D.W. and Barclay, R.L.“A Study of Gap Fillers for Wooden Objects.”Studies in Conservation, Vol. 33, No. 2, 1988, pp. 71–86.
Hatchfield, P.“A Note on a Fill Material for Water Sensitive Objects.”Journal of the American Institute for Conservation, Vol 25, 1986, pp. 93–96.
Phillips, W.W. and Selwyn, J. “Epoxies in Wood Repairs for Historic Buildings.” U.S. Dept. of the Interior, Heritage Conservation and Recreation Service Publication, Number 1, Washington, 1978.
Barclay, R.L. and Grattan, D.W.“A Silicone Rubber/Micro-balloon Mixture for Gap Filling in Wooden Objects.” ICOM Committee for Conservation - Proceedings of 6th Triennial Conference, Sydney, Australia, 1987.
Code of Ethics and Guidance for Practice, International Institute for Conservation - Canadian Group and Canadian Association of Professional Conservators, Ottawa, 1986.
Ciba-Geigy, Araldite AZ-3456 Product Data Sheet, n.d.
Union Carbide Corp., Bakelite Phenolic Microballoons Product Application Bulletin, n.d.
Grattan, D.W. and Barclay, R.L.
Section Index |