OBSERVATIONS ON THE DRYING OF PAPER: FIVE DRYING METHODS AND THE DRYING PROCESS
JANE E. SUGARMAN, & TIMOTHY J. VITALE
6 EXPERIMENT 3: PROLONGED HUMIDIFICATION OF SEVEN PAPERS
To determine whether humidification wets the paper sufficiently to allow complete relaxation before redrying, a study of the humidification stage of the two-stage air-dried–humidification method was undertaken following the procedure described in appendix 2. It was assumed early in this research that the air-dried–humidification method would be a poorly performing drying method, but the results of experiment 1 do not support this conjecture. An investigation of the uptake of moisture in a humidification chamber was conducted to determine (1) how much water is absorbed during humidification and (2) if the water content changes over a prolonged period of exposure to water vapor.
Spraying and ultrasonic humidification treatments consist of the transfer of liquid water, broken into droplets, to the sheet being treated. Because these methods can result in any desired water content, even to the flooded state if continued long enough. Spraying and ultrasonic humidification are to o variable for scientific investigation. Only humidification with water vapor is studied here. It has been widely assumed, that water vapor humidification will result in sufficient water content to plasticize paper and result in a “gentle” flattening.
6.1 RESULTS
Results reported in figure 7 clearly indicate that after 5 days in the humidity chamber (far exceeding the amount of time employed in standard practice) the maximum percent moisture content does not go below 81 � 5% solids or 19% water. After 3 hours the papers were 86 � 4% solids, or 14% water. Swollen with water, fibers in the papers represented in figure 5 are at their fiber saturation points but not beyond. Both values are well above the 63 � 3% solids required for interfiber hydrogen-bonding release.8 At the fiber saturation point there is no water in the paper pores. Thus vapor humidification does not release the fiber-to-fiber network hydrogen bonds.
Fig. 7.
Seven papers humidified for 120 hours at 95% RH
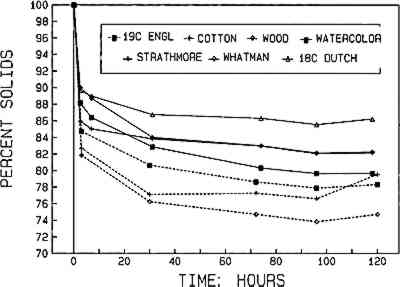 |
Humidification does not result in a sufficient uptake of moisture to put water in the paper pores, which would result in a breakage of fiber-to-fiber hydrogen bonds (Christiansen and Giertz 1966). Humidification with water vapor causes a plasticization of the paper fibers due to the rupture of hydrogen bonds within the fibers. Bond breaking occurs because water is substituted across existing hydrogen bonds. When a single water molecule bridges between hydrogen bonded surfaces, a “new” bond configuration results, which is weaker. Once enough water molecules have been introduced into the bonding site, the “structural” hydrogen bond is lost. The absorption of water onto the hydroxyl-studded cellulose surfaces or across hydrogen bonds in accessible regions (amorphous cellulose) in the microfibrils results in swelling. Swelling opens additional surface and creates more accessible regions, so that more absorption and swelling occur.
Eventually all cellulose surface area, fiber micropores, and accessible hydrogen bonds have water molecules associated with them: The fiber is at the fiber saturation point and completely plasticized. Plasticization is a state in which the rigidity of the fiber, due to “structural” hydrogen bonds between cellulose chains, elementary fibrils, microfibrils, and fibrils, have been disrupted. Plasticization releases stresses that were dried into the fibers when the sheet dried (Rowland 1979).
When rewetting is performed with liquid water, the effects are different (Christiansen and Giertz 1966). Liquid water will eventually saturate the fibers and begin to form a liquid film. The liquid film will eventually fill capillaries at bonding sites and disrupt the fiber-to-fiber hydrogen bonds. If enough water is applied to the sheet, it will reach the flooded state depicted in (stage 1) of figure 6. When the sheet redries, the process of bonding between fiber surfaces is repeated.
The extent of unbonding and the accompanying relaxation of dried-in stresses are greater with liquid water. Humidification does provide fiber relaxation, but only a more thorough wetting breaks a sufficient number of bonds to reform a cockled sheet. In order to allow sufficient relaxation of the paper for replication of original surface texture, liquid water in the form of fine spray or ultrasonic humidification is necessary. It should be noted that first exposure to humidification or rewetting will alter properties such as gloss and smoothness (Wink 1961).
In figure 1 the mean for the air-dried–humidification method appears to be similar in degree of change to the early restraint methods. It is believed, however, that the two drying methods are fundamentally different because the fibers are merely plasticized during vapor humidification. Complete wetting results in breaking fiber-to-fiber bonds and rupturing the fiber network. Properly applied flattening following a thorough rewetting will result in reformation of the network bonds in a new flat configuration. This assertion will be explored in future work.
6.2 IMPLICATIONS FOR TREATMENT
For flattening, when possible, exposure to liquid water—whether, by ultrasonic humidification, or spraying—is preferable to humidification with water vapor because the paper relaxes more with increased wetting. To control the surface quality of the sheet, the object should be placed under restraint as soon as possible, given the condition of the media.
|