METHODS AND MATERIALS FOR FILLING LOSSES ON LACQUER OBJECTS
MARIANNE WEBB
3 FILLS FOR WESTERN LACQUER
3.1 CHARACTERISTICS TO BE CONSIDERED DURING TREATMENT
There are two types of Western lacquer—spirit varnishes and oil varnishes. Both have been known as japanning for at least 200 years. Spirit-based japanning appeared in Europe during the 16th century, while the oil finishes (often with copal resin added) were first developed as a coating for metal in the early 18th century. In the past these two types of japanning have often been mistaken, one for the other, sometimes with disastrous results. Most conservators have encountered examples of alligatored finishes in which an oil varnish has been mistakenly applied over the spirit-based resin surface. Treatment should take into account which type of lacquer has been used.
In no case is it appropriate to use urushi to fill losses in European japanning because they are radically different materials. Occasionally one finds examples of furniture in which Asian lacquer panels have been incorporated. As European materials are used in the construction of these composite objects, it is still inadvisable to use Asian lacquer for repairs. Many times the surface of the Asian lacquer has been recoated with varnish at the time the cabinet was constructed. Now part of an entirely new work of art, these panels can no longer be conserved as Asian objects.
Some fills for japanning are the same as those for urushi-based objects. In nearly all treatments the approach has been to treat the ground and the resin layers separately. For japanned finishes that were made using spirit varnishes, the main concern during conservation is that the solubility of any medium used should be different from the original surface. As these japanned finishes involved a great many natural resins, they often remain soluble for many years, even centuries. Successful treatments have utilized materials with an appearance similar to natural resin, but with different solubility. In general the spirit-based varnishes are not soluble in nonpolar solvents such as mineral spirits or xylene. For japanning that was originally done in a baked oil finish, which tends to be more insoluble, the choice of media and solvents is much greater. Nonetheless, solubility tests should always be carried out prior to commencing work.
3.2 GESSO
The grounds for spirit-based japanning are most often made of rabbit-skin glue or hide glue and whiting, but even contemporaneous literature debates the effectiveness of a ground. Robert Dossie states in the Handmaid to the arts (1764),
One principal variation in the manner of japanning is, the using or omitting any priming or undercoat on the work to be japanned…. There is nevertheless this inconvenience always attending the use of an undercoat, that the japan coats of varnish and color will be constantly liable to be cracked and peeled off by any violence, and will not endure near so long as the bodies japanned in the same manner, but without any such priming.
These observations continue to prove sound, as the frequent losses to this material demonstrate.
Since these objects were first fabricated, the losses have often been filled with the same material as the original: gesso. The disadvantage of this method is that fills would be difficult to remove without damage to the original. If traditional gesso is used, barium sulphate can be added so that at least the fills will be readily apparent when x-radiographed.
In making gesso fills there are a number of cautions. In friable areas it goes without saying that the surrounding area is first consolidated. The original surface surrounding the losses should be protected from the gesso and subsequent sanding with a removable varnish. Due to the high water content, one must take care when applying the gesso not to soak the substrate. A dough is preferable to many layers of liquid gesso, as would be applied in gilding. Since gesso fills shrink on drying, several applications are necessary.
Depending on the circumstances, one might want to vary the strength of the rabbit skin glue considerably. Ballardie (1994) described the use of a very weak pigmented gesso to fill shallow losses in varnish layers of a japanned cabinet prior to cleaning. In this particular case the gesso was strong enough to support the surrounding fragile japanning, yet easily removed as it was not in direct contact with the original ground.
An English japanned clock case with a casein ground was treated by Bigelow (1990). Here a 10% rabbit-skin glue and whiting gesso was used as a reversible infill for losses to the ground only. Japanning layers were infilled with different materials.
A traditional approach does not always need to be used. For a gesso ground or one with similar properties, polyvinyl alcohol and whiting can also be used, as outlined in the urushi section of this article. On a late 17th-century cabinet in the Royal Ontario Museum Collection many of the raised decorations were lost or crumbling. After consolidation, the losses were infilled with 6% polyvinyl alcohol in water, whiting, and dry pigments (Webb 1997).
3.3 PAPIER-M�CH�
Eighteenth- and 19th-century European and American manufacturers took advantage of new methods to produce hard paper boards for japanning. Various oil formulations, usually consisting of boiled linseed oil, burnt umber, red lead, and often asphaltum were applied directly to the dried boards, then stoved to dry the coating (Dossie 1764). A ground layer was not used in this method. If a gesso ground is found, it suggests that the object was produced by other means.
Losses to this material usually involve the paper substrate as well as the lacquer layers. As the oil varnish and the papier-m�ch� are such different materials, it is advisable to treat these two layers separately.
At the Royal Ontario Museum, the simple method of building up layers of paper and methyl cellulose has been used with success. Good quality Japanese paper was used, and each layer was allowed to dry completely before the next was applied. Fills on a sewing table done with this method appear unchanged after 10 years (fig. 5).
Fig. 5.
An infill on papier-m�ch� using Japanese tissue and wheat starch paste built in layers
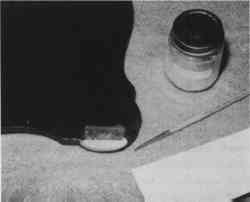 |
Other conservators have found that the preparation of papier-m�ch� panels in a method similar to the original works well. Van der Reyden and Williams (1986) have outlined a method involving taking a mold of an intact area similar to the area of loss. High-quality oriental paper coated with wheat starch paste is pressed into the mold and baked at 100�F. The baked paper can be carved to its final shape, then adhered into place with wheat starch paste. In both examples the japanned surface area was imitated using different materials.
3.4 WAX
Although it has been used in the past (Moir 1979), for the most part the author would avoid wax formulations where there are losses of the paper substrate or a gesso ground. As with urushi, the use of a wax as a fill makes it extremely difficult to carry out repairs using other materials. Beeswax, carnauba, or microcrystalline wax formulations such as those given in the urushi section of this article could be used for fills that involve only the surface layer.
Often many japanned pieces of furniture include raised areas that were applied after the basic japanning was complete. The original use of gesso and other incompatible materials over the varnish contributes to their frequent loss. Wax has been used successfully to recreate or fill these losses. In this case the wax is sitting on top of the original japanned surface, as are the raised areas of the original. Hill (1976) describes the use of microcrystalline wax, rottenstone, and pigment for this purpose on the Pimm highboy.
3.5 PARALOID B-72 AND MICROBALLOONS
The author has also experimented with the use of 25% Paraloid B-72 or B-67 bulked with a small amount of the finest grade of glass microballoons and black pigment to fill small losses. This formula works well for the losses around mother-of-pearl decoration, and for a larger area it should also be very successful.
3.6 IMITATION OF SURFACE LAYER
3.6.1 OIL PAINTS
Oil paints on japanning have been used extensively in the past, but they have disadvantages. Besides being irreversible, they can accelerate deterioration when applied over a spirit varnish. As the oil continues to dry and shrink, it pulls the japanning off of the surface. Although more recently oil paints have been used over a separating layer of wax or Paraloid B-72 (Beale 1994), the author is still wary of their use .
3.6.2 ACRYLICS
On japanned finishes that were made using spirit varnishes, the main concern is that any inpainting medium should be soluble in a solvent different from that for the original surface. Successful treatments have utilized materials with an appearance similar to natural resin but that dissolve in different materials. For this reason the acrylic emulsions that were suggested for use with Asian lacquer are not always suitable for this type of japanning.
For japanning that was originally done in a baked oil finish, the choice of inpainting media is much greater. Here acrylic paints such as Liquitex are again suitable.
For both types of japanning, Paraloid B-67 or B-72 can be mixed with dye to achieve a good approximation of the aged varnishes. Orasol dyes by Ciba-Geigy are particularly useful for this purpose. These dyed resins can be applied in layers over a ground of traditional gesso, acrylic gesso, or polyvinyl alcohol and whiting to build up the fills to surface level. Either synthetic resin can be used, but the gloss of Paraloid B-67 is more similar to the original japanned surface. Bigelow (1990) has described the use of Paraloid B-72 mixed with dry pigment to inpaint areas on a clock case with opaque japanned surfaces. A similar clock conserved by Park (1994) utilized the same method with Paraloid B-67 but with added microcrystalline wax to give a sheen similar to the japanned surface.
For the most part the author's inpainting is done in an acrylic medium such as Liquitex following the application of a barrier coat. Losses in gilding can be imitated well using gloss medium and Afflair Lustre pigments (mica-based). Other media such as Paraloid B-72, B-67, or PVA AYAF and dry pigments in a standard inpainting approach have also been used to imitate the surface successfully (figs. 6, 7).
Fig. 6.
English papier m�ch� sewing table showing Japanese paper infill before inpainting
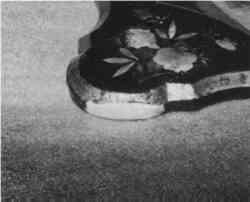 |
Fig. 7.
Same infill as in figure 6 after inpainting with Liquitex paints and Liquitex medium with micabased pigments
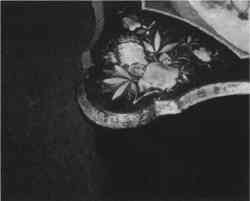 |
3.7 OTHER METHODS
Bruno (1996), working on a Mexican lacquer tray, used an interesting technique developed at the Freer Gallery of Art. This technique used Parafilm M, an American Can Company product that the Canadian Conservation Institute tested and found to be a blend of polyethylene and polyisobutylene. An isolating layer of Paraloid B-72 was applied to the loss prior to trimming the Parafilm to shape. Then, with a heated spatula and silicone release paper, layers of parafilm were built up to the level of the original surface. The excess was trimmed away with a scalpel. Inpainting, to match the surrounding opaque surface, was done using Liquitex acrylics. An advantage of this method is that the fill is particularly easy to reverse; unfortunately, the Parafilm does not work well for imitating translucent layers.
3.8 VARNISHES
Often japanned furniture is revarnished to help integrate the fills into the overall appearance of the object. Over the centuries revarnishing has often resulted in an accumulation of dark yellow and brown layers. Even the use of synthetic resins can have problems. While Paraloid B-72 can be dissolved in many solvents that are different from solvents that work for the original, its appearance is very unnatural and has given several pieces of japanned furniture a look of “plastic.”
Occasionally the author has used a synthetic resin in a very thin coat but remains convinced that it does not have the rich luster of true japanning. The final result was disappointing. This overall varnishing of japanned furniture should be avoided if possible. Satisfactory, but not always invisible, fills can be achieved using the methods outlined above.
3.9 TRADITIONAL JAPANNING
The use of traditional japanning to repair small losses might make it difficult to differentiate from the original and to reverse the fill in future years. Traditional japanning, however, may be the best option for replacing missing parts or large isolated areas of a piece of furniture.
The difficulty in reproducing the original finish arises in determining exactly what methods and materials were used. Even a cursory look at the contemporary literature will demonstrate the complicated nature of these finishes. However, with chemical analysis of the existing japanning and a thorough understanding of the original formulas, good quality japanning can be reproduced today.
Walch (1993) outlined her investigations of several methods used in the past. Her research and the analysis done by Koller (1993) have contributed to the understanding of the numerous resins used in these formulations. Their work on the Munich Residenz cabinet revealed that what looked like a simple red japan was, in fact, quite complicated (Walch et al. 1996). Synthetic cinnabar was applied to the wood in a seed lac preparation, followed by layers of a more complicated translucent varnish composed of sandarac, larch turpentine resin, mastic, and camphor. The addition of lake cochineal and cochineal dye to final layers of the original enhanced the red color in a cost-effective manner. The lost panels of the Munich Residenz cabinet have now been recreated using the technique discovered through this research.
3.10 CONCLUSIONS
To develop new materials and methods of fills that are visually compatible with either type of japanning, understanding the original processes is paramount. Through analysis, examining texts, and reproducing original recipes, we come to the realization that often the method of application is as important as the materials used. With an improved understanding of technique we will be able to develop better fills in the future.
|