ANALYSIS OF GYPSUM-CONTAINING LIME MORTARS: POSSIBLE ERRORS DUE TO THE USE OF DIFFERENT DRYING CONDITIONS
A. ELENA CHAROLA, & SILVIA A. CENTENO
ABSTRACT—Analyses of mortars require that they be dried to eliminate sorbed moisture. There is no consensus regarding the temperature at which the samples need to be dried. If mortars contain gypsum, hydration water may also be lost depending upon the drying temperature. The results presented show that the dehydration behavior of gypsum is influenced by the presence of other materials. The errors introduced into the results of the analysis as a function of the drying temperature chosen are discussed.
TITRE—L'analyse des mortiers � base de chaux et contenant du gypse: erreurs possibles dues � l'utilisation de diff�rentes conditions de s�chage. R�SUM�—L'analyse des mortiers n�cessite que ceux-ci soient s�ch�s afin d'�liminer l'humidit� sorb�e. Il n'existe aucun consensus concernant la temp�rature � laquelle les �chantillons doivent �tre s�ch�s. Si les mortiers contiennent du gypse, le degr� d'hydratation peut �galement �tre affect� par la temp�rature de s�chage. Les r�sultats des tests d�montrent que la d�shydratation du gypse est influenc�e par la pr�sence d'autres mat�riaux. On pr�sente aussi les erreurs qui peuvent �tre caus�es dans les r�sultats de l'analyse en fonction des diff�rentes temp�ratures de s�chage.
TITULO—An�lisis de morteros de cal que contienen yeso: posibles errores debidos al uso de diferentes condiciones de secado. RESUMEN—Los an�lisis de morteros requieren que se los seque para eliminar la humedad sorbida. No hay consenso con respecto a la temperatura a la cual deben secarse las muestras. Si los morteros contienen yeso, el agua de hidrataci�n tambi�n puede perderse dependiendo de la temperatura de secado. Los resultados que se presentan muestran que la presencia de otros materiales puede influir en la deshidrataci�n del yeso. Se discuten los errores que se introducen en los resultados de los an�lisis en funci�n de la temperatura que se elige para el secado.
1 INTRODUCTION
Chemical analysis usually requires that samples be dried to eliminate sorbed moisture so that the results can be reported as a function of the dry weight of the sample. This requirement also applies to mortar analysis, especially since a high moisture content can be indicative of the presence of contaminating soluble salts. In traditional chemical analysis, samples are dried at 105�C, this temperature having been chosen on the basis of the 100�C evaporation point of water at standard pressure conditions.
Some procedures for the analysis of historic mortars use this traditional approach (Callebaut et al. 1999). However, in the case of historic materials, which might presumably have received a conservation treatment in the past, it has been suggested that a drying temperature of 60�C is more appropriate since it would prevent decomposition of these organic compounds (NORMAL 1988, NORMAL 1989b). Even this temperature was considered inappropriate for the special case of historic gypsum mortars, given the decomposition that gypsum suffers at temperatures above 40�C (Mehlmann 1993). Nonetheless, practical experience found that drying gypsum-containing mortar samples at ~55�C for only 16 hours prevented dehydration of gypsum, provided the samples were not damp and only three samples were dried at a time (Dupas 2001). Furthermore, some procedures do not specify a drying temperature (NORMAL 1989a), while in other cases both temperature and drying time are specified—e.g., sample is dried at 110�C for 24 hours for a simple acid attack and determination of sand and fines; or at 60�C for 48 hours for the calcimetric determination of CO2(Teutonico 1988).
This article describes the results obtained during an investigation of the drying conditions commonly used in the analysis of mortars following standard laboratory procedures, using simple mixtures of fine silica, calcite, and gypsum powder, to determine the magnitude of the errors introduced into calculations from the incomplete drying of the sample or the partial decomposition of gypsum.
2 EXPERIMENTAL
A flowchart of the three experimental protocols is presented in the appendix to this paper.
2.1 GYPSUM
In the first place, the behavior of pure gypsum powder (calcium sulfate dihydrate 98%, Aldrich) was studied when dried at ~0% RH at room temperature, and at 40�C, 60�C, and 105�C. The ~0% RH was obtained using a laboratory desiccator containing Drierite. This product, based on specially processed calcium sulfate, is capable of taking up 14% of its weight in water. In practice, it is estimated that the actual relative humidity is below 5% for standard glass laboratory desiccators.
The drying temperatures were set on a commercial laboratory drying oven. The samples, weighing ~3 g, were left at these conditions until the relative change in weight was less than or equal to 0.003%. Two of these samples, those dried at 0% RH and at 105�C, were then conditioned for 20 days at 75% RH to determine their moisture absorption.
2.2 GYPSUM-CONTAINING MIXTURES
At the same time, mixtures of gypsum with powdered calcite (calcium carbonate, certified ACS, Fisher Scientific) or silica (floated, Fisher Scientific, particle size approximately 240 mesh) were dried at ~0% RH, 40�C, 60�C, and 105�C to determine the effect a second component would have upon the dehydration of gypsum. For this purpose, 5% by weight of gypsum was mixed with each of the powdered materials. Pure calcite and pure silica samples were also dried as controls. All samples, weighing approximately 3 g total, were left to dry until the relative change in weight was less than or equal to 0.003%.
Of the above mixtures, those dried at 60�C, as well as the corresponding sample of pure gypsum, were redried at 105�C for 11 days after having been kept in a closed container in laboratory conditions for about a month. After drying they were re-exposed to ambient conditions in the laboratory, and their weight increase was monitored. It was found that after four days the weight of the samples changed (on the order of 0.05%) as a function of the fluctuations of relative humidity in the laboratory, and the weight monitoring was discontinued.
2.3 GYPSUM-AND SALT-CONTAINING MIXTURES
A third set of samples was prepared by mixing key components of a real mortar. Approximately equal amounts of silica and calcite—about 1.5 g of each—for the control were mixed and labeled as C. The set was completed by adding 5% of gypsum (~0.15 g) to some samples (C + G); 2% of sodium chloride to others (C + H for halite); both 5% gypsum and 2% sodium chloride (~0.06 g) to a third group (C + G + H); and both 5% gypsum and 1% sodium sulfate (~0.03 g) to the fourth group (C + G + T for thenardite). All weighings were carried out to 0.01 mg. The actual number of millimoles contained in the samples were calculated from these weighings.
These samples were first conditioned at 75% RH for two weeks and then dried at 40�C or at 105�C, or in a desiccator at approximately 0% RH, until the relative change in weight was less than or equal to 0.003%.
3 RESULTS AND DISCUSSION
3.1 GYPSUM
The results, expressed as millimoles of water per mole of gypsum (mM water/M gypsum) for the drying of pure gypsum powder under different conditions and the subsequent moisture absorption for those samples dried at ~0% RH and at 105�C upon 20-day conditioning at 75% RH, are presented in table 1.
The results clearly show that under normal laboratory conditions, gypsum dehydrates partially, i.e.,
Table .
Moisture Loss Expressed as mM Water/M Gypsum
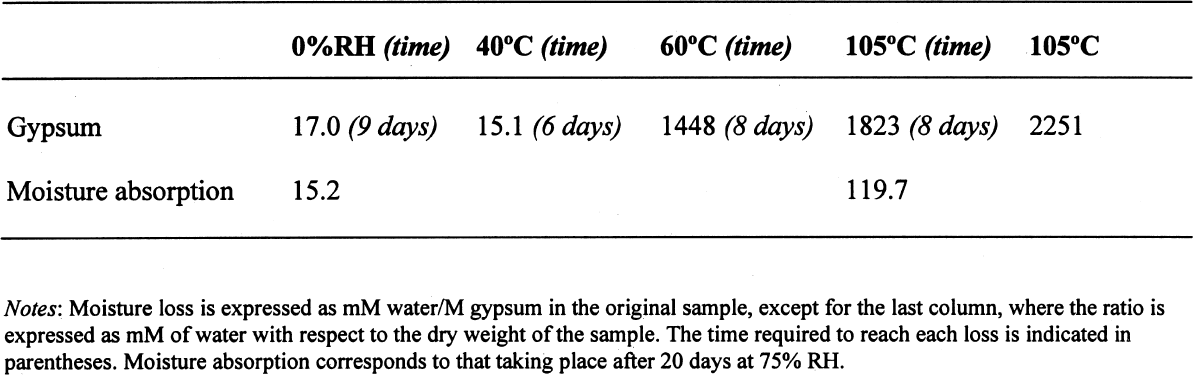 |
converting to the metastable hemihydrate CaSO4.1/2H2O at 60�C, and dehydrates most probably into the thermodynamically stable phase anhydrite CaSO4 when heated to 105�C. The reaction can be written as:
The sequence of these dehydration reactions has been previously observed and described (Macdonald 1953; Palache et al. 1966; Deer et al. 1975; Ullmanns 1976). Gypsum only lost sorbed moisture when kept at ~0% RH, and this amount was recovered when conditioned at 75%RH. The sample dried at 105�C apparently did not reabsorb any hydration water.
3.2 GYPSUM-CONTAINING MIXTURES
The results of the gypsum mixtures with powdered calcite or silica, as well as of the control samples, are presented in table 2.
The first interesting observation is that the samples dried at 105�C lost practically the same amount of moisture as those at 60�C, or even less. These results could be explained by the fact that these samples were dried together with the abovementioned gypsum sample, and thus the high amount of moisture lost by this material in addition to that lost by the mixtures prevented further desorption or dehydration from these last samples during the week-long drying. It appears that although the oven does have a ventilation opening and equilibration of absolute humidity with the environment may take place when the door is opened, this condition is not sufficient to eliminate the released moisture when there are many samples present (in our experiment, five samples were in the oven simultaneously). The ease of moisture absorption or desorption depends on the nature of the sample, and since it has been shown that the joint presence of a hydrating salt and a nonhydrating material enhances moisture absorption (Charola and Weber 1992), it appears that it may also presumably hinder dehydration of the hydrated salt.
At ~0% RH, calcite powder loses the same amount of moisture as at 60�C, whereas the silica powder shows that it requires some heating to lose the sorbed moisture.
The weight loss and gain of the samples (previously dried at 60�C) redried for 11 days at 105�C and re-exposed to laboratory conditions for four days, the time it took for samples to re-equalize with ambient conditions, are presented in table 3.
Since these samples had been previously dried at 60�C, the amount of moisture lost corresponds to the difference in moisture loss between these two drying temperatures. Gypsum nearly recovered all the moisture lost during the 11-day drying, corresponding to
Table .
Moisture Loss Expressed as mM Water/M Material in the Original Sample
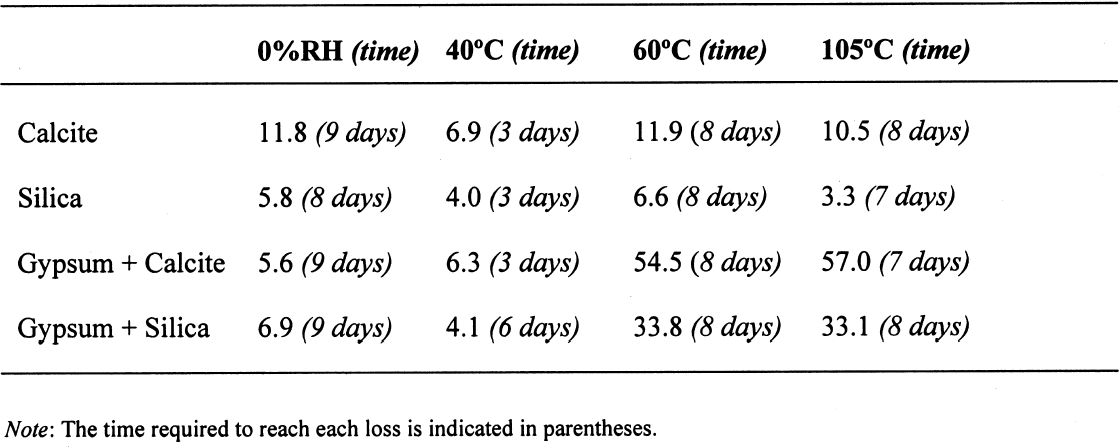 |
Table .
Amount of Moisture, Expressed as mM Water/M Material, Lost during 11 Days of Drying at 105�C and Gained upon Re-exposure to Laboratory Conditions during Four Days, by Pure Gypsum or Mixed with Calcite or Silica
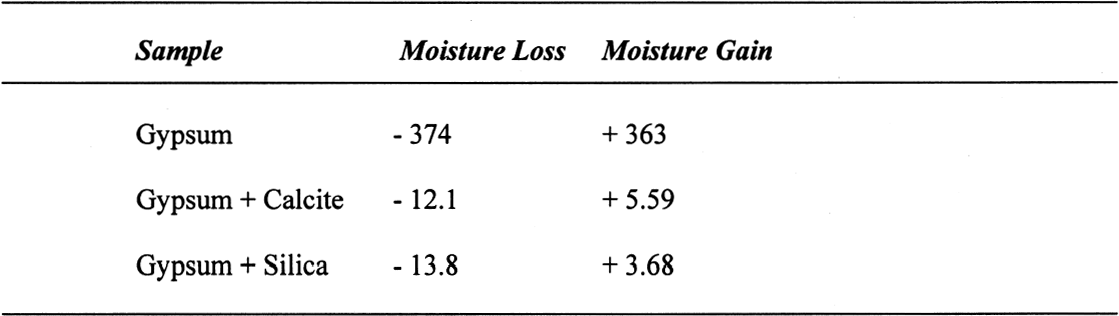 |
the loss of the 0.5 molecule of the hemihydrate (the value is not exactly 500 because the weights are not standardized against the dry weight—see table 1) and suggesting, by the ease of rehydration, that the anhydrite obtained was the metastable form, called soluble anhydrite or γ-CaSO4, which rehydrates readily to hemihydrate (Deer et al. 1975). However, it contrasts significantly with the previously obtained data of the sample set at 75% RH (table I). In this case, it would appear that the stable anhydrite form, or β-CaSO4, is formed, since it does not rehydrate that easily. Conditions influencing this dehydration are probably the varying amounts of moisture present in the oven during drying.
3.3 GYPSUM-AND SALT-CONTAINING MIXTURES
The samples containing soluble salts, preconditioned at 75% RH and then dried in a desiccator at ~0% RH, arrived at their minimum weight in two days. This result can be explained by the loss of absorption power of the desiccant agent, even though there was no visual color change in the cobalt salt used as indicator. Cobalt salts will change color from blue (dehydrated state) to pink (hydrated state) when the relative humidity is over 30%.
The corresponding samples dried in the oven, at 40�C and 105�C, took about seven to eight days to reach this point. The moisture loss, expressed as the ratio of millimoles of water to the total number of moles of material in the original sample, is presented in table 4.
As indicated previously, the samples in the desiccator did not lose all their moisture, although the moisture loss follows the overall trend.
The moisture loss for the control sample is equivalent to that lost “theoretically,” as calculated
Table .
Moisture Loss Expressed as mM Water/M Material in the Original Sample
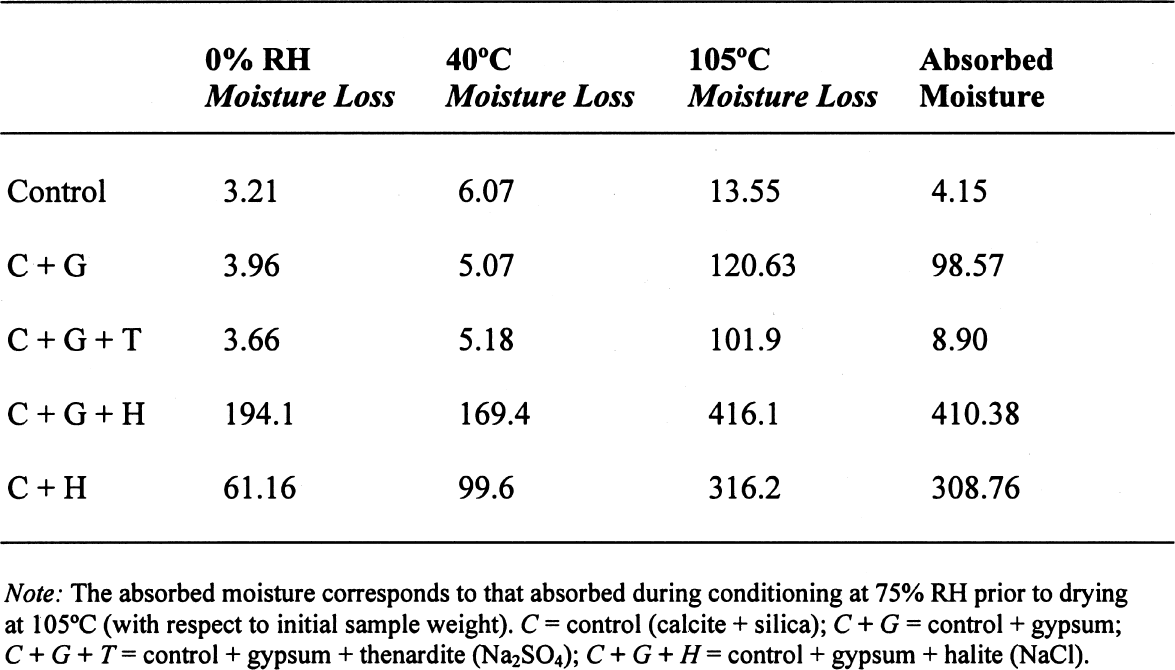 |
from the moisture loss of the individual calcite and silica samples reported in table 2 (see next section for an example of the calculation)—that is, approximately 8.88 mM/M sample, plus the moisture absorbed during conditioning at 75% RH.
A similar behavior is observed for the sample containing gypsum, the difference between the lost and absorbed moisture reaching some 22 mM water/M sample, fairly close to the measured 17 mM water/M gypsum as reported in table 1. This finding clearly shows that gypsum does not dehydrate completely at 105�C when mixed with another material and if a relatively high amount of water vapor is present in the oven, as discussed for the previous samples.
For samples containing NaCl, the hygroscopicity of sodium chloride (NaCl) at 75% RH is clearly evident, and the amount of moisture lost corresponds practically entirely to the moisture sorbed by this salt.
Finally, the presence of sodium sulfate in the mixture reduces by nearly tenfold the amount of moisture absorbed, though the amount lost by heating is similar to the sample without this salt. This unexpected behavior requires further research that is outside the scope of the present article.
3.4 ANALYSIS OF ERRORS
From the data in tables 1 and 2, the amount of sorbed moisture for the different powders can be calculated. For example, silica powder lost approximately 7 mM of sorbed water per mole of silica, while gypsum lost some 17 mM of water per mole of gypsum. The sample, weighing 3.09719 g, was constituted of 0.15486 g of gypsum and 2.94233 g of silica, corresponding to 0.8994 and 48.9898 mM, respectively. The theoretical loss of sorbed moisture would correspond to 0.35973 mM, the sum of 0.01529 mM of water from the gypsum and 0.34293 mM of water from the silica. This sum corresponds to a calculated weight loss of 6.46 mg. In the case of calcite, 12 mM of water per mole of calcite were used for the calculations. The results obtained for these calculations, as well as the actual measurements obtained, are presented in table 5.
The difference obtained between the calculated
Table .
Comparison of Measured and Calculated Weight Losses
 |
and the measured amount differs by around 3 mg for samples dried at 40�C, indicating that the sample has not dried completely. Considering that the total weight of the sample is around 3 g, this difference represents a relative error of approximately 0.1%.
On the other hand, for samples dried at 60�C, if the decomposition of the gypsum is taken into account, the relative error decreases to around 0.05%, taking an average difference of 1.5 mg. However, if the decomposition of the gypsum is not taken into account, i.e., only assuming loss of adsorbed water as calculated for 40�C, the differences obtained would be –23.39 mg for the silica mixture and –20.91 mg for the calcite mixture, corresponding to an overestimation of the moisture content and increasing the relative error tenfold (~0.7%).
A similar analysis can be done for some of the samples reported in table 4. If the weight loss is calculated from the initial weight of the sample, i.e., prior to conditioning, the data presented in table 6 are obtained.
While the control samples behave as expected, those that contain gypsum do not follow a predictable path. The gypsum present, dried at 105�C, loses some hydration water, and from the data obtained, it would appear that approximately one-half of the gypsum present dehydrates to the hemihydrate. This introduces a relative error of 0.3%, whether it is assumed that the gypsum does or does not dehydrate to hemihydrate. Under the same conditions, the control sample shows a relative error of 0.01%.
How critical these errors are depends on the accuracy with which the mortar analyses are carried out. Comparing the methods mentioned in the introduction, table 7 can be constructed.
All methods mentioned use precisions that result in relative errors below the one observed, resulting either from insufficient drying or from gypsum decomposition.
4 CONCLUSIONS
Clearly the most important results obtained are that the behavior of gypsum toward moisture take-up is, in some cases, modified by the presence of other components in the mixture and that this behavior will depend on the nature of the latter. Furthermore, the dehydration behavior of gypsum will vary depending on the amount of water vapor present in the oven—those without ventilation—from the drying of the samples. If there is no significant amount of moisture in the oven, gypsum will dehydrate to hemihydrate above 40�C and to insoluble anhydrite at 105�C. If some moisture is present at this temperature, soluble anhydrite may form, which tends to rehydrate fairly rapidly if not kept in an appropriate desiccator. As mentioned, the stability relations between these phases, hemihydrate-soluble anhydrite and anhydrite proper, are not well defined
Table .
Comparison of Measured and Calculated Weight Losses at 105�C
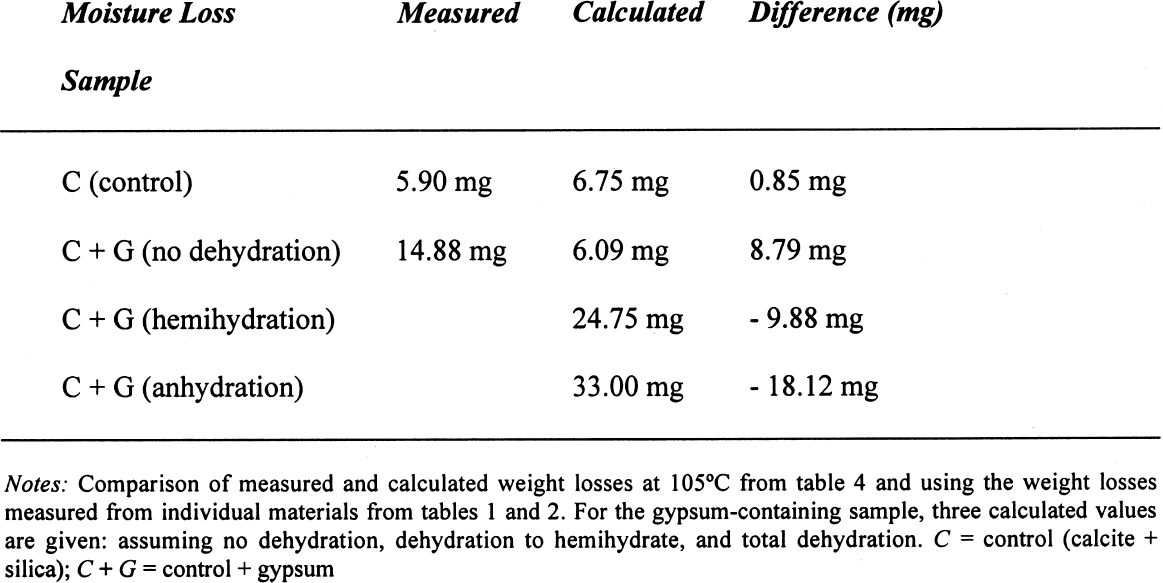 |
Table .
Various Analytical Methods Currently in Use for Mortar Analysis. Sample Size, Measurement Precision, and Approximate Relative Error of the Approach
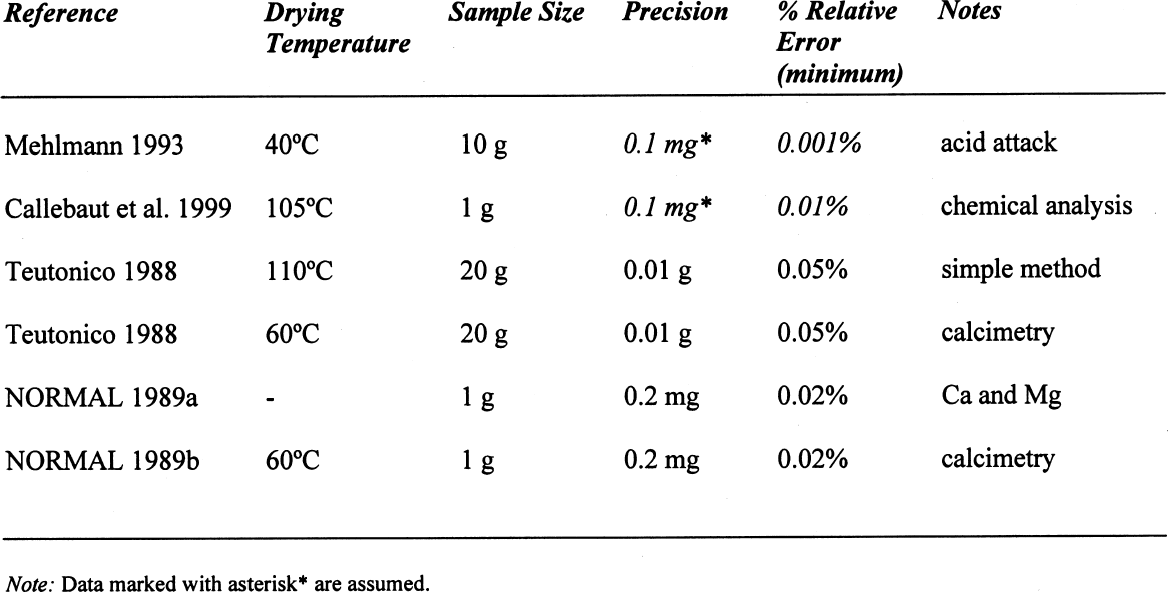 |
(Palache et al. 1966). If a high amount of moisture is present in the oven, gypsum may only partially dehydrate to hemihydrate even at 105�C. The conditions under which analysis of gypsum-containing mortars is carried out are therefore critical.
Furthermore, several practical conclusions could also be reached. The first one is that the drying procedure may not be as fast as supposed, especially if samples contain a relatively high amount of moisture or gypsum. The usual practice suggests 24-hour drying at 105�C, weighing and redrying for another 24-hour period to confirm the stability of the weighing. Normativa Manufatti Lapidei (NORMAL) procedures just indicate the maximum allowable change in two subsequent weighings but do not even indicate an approximate length of time required to reach this value. In our experiments, this process took at least one week. This time frame is an important consideration when planning to carry out a set of mortar analyses. In particular, architectural conservators who do not routinely carry out analyses but do so only on an ad hoc basis need to take this time frame into account.
A similar effect was noticed when samples of this type were left to dehydrate in the desiccator. Given the nature of the desiccant used, the amount, exposed surface, and size of the desiccator will determine its drying efficiency. And since the indicator color change occurs only above 30% RH, it is clear that samples containing a high amount of moisture are not dried completely. Therefore the second practical recommendation is that to keep samples dry, they should be kept to a minimum, and the desiccant in dessicators needs to be changed periodically, particularly when larger “storage” cabinet dessicators are used.
Finally, the issue of the error introduced into the analysis results, depending on the drying temperature used, has to be considered. At 40�C, it has been shown that samples do not dry out completely. At higher temperatures, gypsum dehydrates in an unpredictable way when large amounts of moisture or other salts are present. Therefore, the analyst needs to consider the aim of the analysis he is performing and take into account the nature of the sample he is analyzing before deciding the temperature at which the samples should be dried.
APPENDIX
APPENDIX
Flowchart of the three main experimental protocols used. Symbols (* or **) indicate subsequent treatment listed below.
Table .
Appendix Flowchart
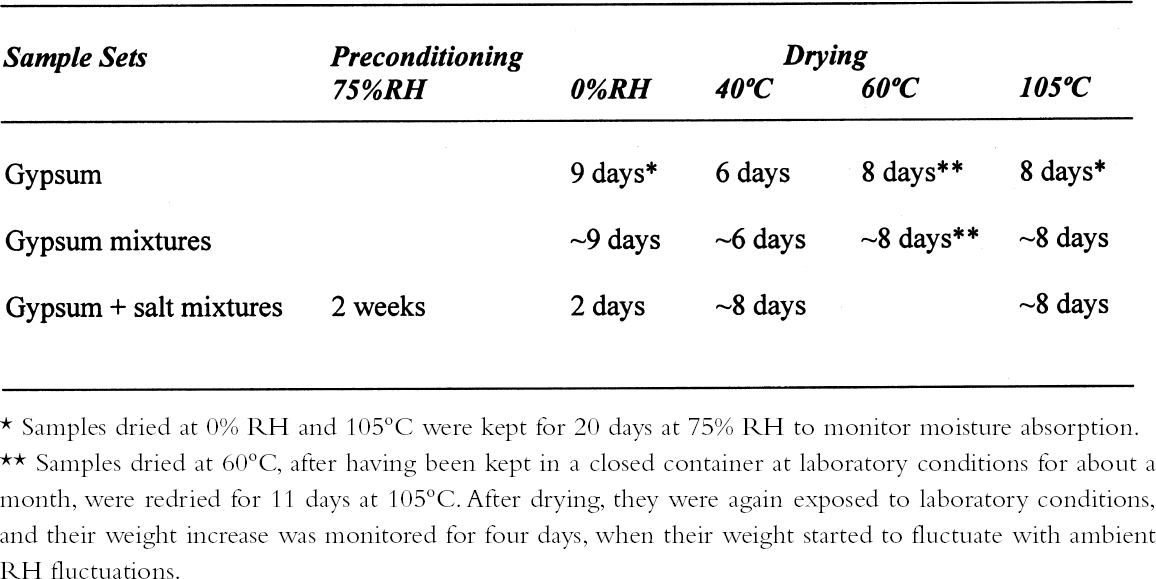 |
ACKNOWLEDGEMENTS
The authors would like to thank Michel Dupas, recently retired from the Institut Royal du Patrimoine Artistique–Koninklijk Instituut voor her Kunstpatrimonium (IRPA-KIK), Brussels, for his thorough revision of the paper and his valuable comments. Also to be thanked for valuable comments and suggestions to improve the text are Dr. Margaret Thomson, Chemical Lime, Boulder City, Nev.; Dr. Eddy DeWitte, IRPA-KIK, Brussels, Belgium; and Dr. Michael Steiger, Universit�t Hamburg, Germany.
LIST OF SUPPLIERSDrieriteFisher Scientific, www.fischersci.com
REFERENCES
Callebaut, K., W.Viaene, K.Van Balen, and R.Otthenburgs. 1999. Petrographical, mineralogical and chemical investigation of 17th and 19th century lime mortars in the St.-Michael's Church (Leuven, Belgium). International Journal for Restoration of Buildings and Monuments6(5):523–42.
Charola, A. E., and J.Weber. 1992. The hydrationdehydration mechanism of sodium sulphate. In 7th International Congress on the Deterioration and Conservation of Stone, ed. J. DelgadoRodrigues et al. Lisbon: Laboratorio Nacional de Engenharia Civil. 581–90.
Deer, W. A., R. A.Howie, and J.Zussman. 1975. Rockforming minerals, vol. 5. London: Longman. 205–11.
Dupas, M.2001. Personal communication. Institut Royal du Patrimoine Artistique, Brussels, Belgium.
Macdonald, G. J. F.1953. Anhydrite-gypsum equilibrium relations. American Journal of Science251:884–98.
Mehlmann, M.1993. Bestimmung von chemischmineralogischen Kennwerte sowie Untersuchungsmethoden. Chap. 3, pt. A. In M�rtel und Steinerg�nzungsstoffe in der Denkmalpflege,ed. D.Kn�fel and P.Schubert. Special issue of the BMT-Verbundforschung zur Denkmalpflege. Berlin: Ernst & Sohn. 39–53.
NORMAL. 1988. Composizione chimica dei materiali lapidei. Raccomandazioni NORMAL, 28/88. Rome: CNR Centro di Studio di Milano e Roma sulle cause di deperimento e sui metodi di conservazione delle opere d'arte and Istituto Centrale per il Restauro.
NORMAL. 1989a. Determinazione della calce e della magnesia residue. Raccomandazioni NORMAL, 31/89. Rome: CNR Centro di Studio di Milano e Roma sulle cause di deperimento e sui metodi di conservazione delle opere d'arte and Istituto Centrale per il Restauro.
NORMAL. 1989b. Determinazione gas volumetrica della CO2. Raccomandazioni NORMAL, 32/89. Rome: CNR Centro di Studio di Milano e Roma sulle cause di deperimento e sui metodi di conservazione delle opere d'arte and Istituto Centrale per il Restauro.
Palache, C., H.Berman, and C.Frondel. 1966. The system of mineralogy of J. D. Dana and E. S. Dana, vol. 2. New York: John Wiley. 484.
Teutonico, J. M.1988. A laboratory manual for architectural conservators. Rome: ICCROM.
Ullmanns Encyklop�die der technischen Chemie. 1976. Weinheim, Germany: Verlag Chemie. 12:291–93.
AUTHOR INFORMATION
A. ELENA CHAROLA obtained her degree in chemistry from the Universidad Nacional de La Plata in her native Argentina. She completed her postdoctoral work at New York University and stayed in the United States, becoming a citizen 20 years ago. She served as associate chemist in the Department of Objects Conservation at the Metropolitan Museum of Art in New York; scientific advisor at the International Center for the Study of the Preservation and Restoration of Cultural Property (ICCROM) in Rome; and consultant to the Easter Island Program for World Monuments Fund (WMF). Since her return to the United States some 10 years ago, she has continued as technical consultant to WMF, including working on projects in other countries (Torre de Belem and Mosteiro dos Jer�nimos in Lisbon, and Nemrut Dag in Turkey) while being an independent consultant in conservation. She has been lecturer in advanced architectural conservation in the graduate program in historic preservation, University of Pennsylvania, and national chair of the Brick Masonry Specialty Committee of US/ICOMOS since 1996. Address: 3618 Hamilton St., Philadelphia, Pa. 19104
SILVIA A. CENTENO received her Ph.D. in chemistry from the Universidad Nacional de La Plata in Argentina in 1994. In 1995 she was awarded an L.W. Frohlich Fellowship in Conservation at the Sherman Fairchild Center for Objects Conservation, Metropolitan Museum of Art in New York, to work on the investigation of pre-Columbian metalwork from Peru. From 1997 to 2001 she continued to be involved in various research projects in conservation at the MMA. In 2001 she was appointed associate scientist at the Sherman Fairchild Center for Works on Paper and Photograph Conservation and at the Sherman Fairchild Paintings Conservation Center (MMA). Her principal interests include the technical examination of works on paper and paintings by nondestructive techniques. Address: Sherman Fairchild Paintings Conservation Center, The Metropolitan Museum of Art, 1000 Fifth Ave., New York, N.Y. 10028-0198
Section Index |