LITERATURE REVIEW: THE USE OF PARALOID B-72 AS A SURFACE CONSOLIDANT FOR STAINED GLASS
SASHA CHAPMAN, & DAVID MASON
2 DESIRABLE CHARACTERISTICS OF A CONSOLIDANT FOR STAINED GLASS
In general terms, an appropriate consolidation treatment for stained glass may be required to improve the adhesion of the paint or painted layer to the glass substrate; improve cohesion of corroded layers of glass paint or stain; be able to cope with thermal and humidity conditions present at the site; possess excellent light-aging characteristics; be resistant to chemical attack; have minimal visual impact on the glass (i.e., not change the color, opacity, or refractive index of the painted layer); possess flow properties that enable it to penetrate the areas of loose paint (i.e., low viscosity and high surface tension); be chemically neutral, and remain so over time; be resistant to biodegradation; possess good application and handling characteristics; and be reversible (or at least not impede retreatment).
In practice, the deterioration of paint on stained glass may involve different kinds of physical and chemical processes, depending on the way in which the stained glass is colored and fired. These processes can range from disaggregation of a fired surface layer and detachment from the glass substrate to lifting of flakes of applied paint. The consolidant must therefore be responsive to the particular nature of the glass in question and its degradation. This requirement makes it difficult to prescribe a single treatment that will work for all situations.
2.1 THE CONSOLIDANTS
Polymers used as consolidants can be divided into two main groups: natural and synthetic. Some natural polymers are relatively stable and have been used in the past for glass repair (Davison 1984). There has been some recent interest in and comparative studies of the potential of natural wax mixtures (beeswax, carnauba wax) for the consolidation of glass paint, and the suitability of these is being monitored in situ (M�ller 1984; Forberg and Bornschein 1996). However, synthetic polymers are generally preferred in conservation on account of the large body of data, acquired over many decades of experimental and laboratory research, that support their stability and other favorable properties. Some synthetics, notably the acrylics, show good aging characteristics. Other synthetic resins—for example, soluble nylon and polyvinyl acetate—are unsuitable, as they can attract dust, which is an undesirable characteristic in a consolidant. In the case of polyvinyl acetate, which has a low glass transition point (Tg) of 28�C, there is also a tendency for the material to cold flow (Newton and Davison 1989).1
For the consolidation of historic stained glass, two broad types of synthetic resin system have been chiefly reported in the literature: epoxies and acrylics. Other materials, such as polyurethanes, have also been used experimentally.
2.1.1 Epoxies
Following early concerns about yellowing and degradation of the resin over time, tests reported the availability of epoxy resin systems that possess acceptable lightfastness and clarity (Tennent 1979; Down 1986). A number of epoxies have been successfully employed, chiefly as adhesives and gap fillers for broken glass fragments (Notman and Tennent 1980; Jackson 1982; Davison 1984; De Henau and Fontaine-Hodiamont 1991). Less successful has been the use of epoxy resins dissolved in solvents such as acetone, or low-viscosity room-temperature–curing epoxies such as Ablebond 342-1, as consolidants for painted glass and grisaille (Weintraub and Greenland 1984; Cole 1989; Femenella 1994; Strobl 1999).
2.1.2 Acrylics
The monomers from which acrylic polymers are made fall into two groups: acrylates and methacrylates. Polymethacrylates were among the first synthetic resins used to coat glass (Bettembourg 1976; Newton and Seddon 1999) and as consolidants are still among the most popular. The Paraloid (formerly Acryloid in the U.S.) resins, discussed more fully below, are perhaps the best known.
2.1.3 Other Materials
A third class of materials, polymers formed by reaction of a polyisocyanate with a polyacrylate, and sometimes categorized in the literature as polyurethanes, has been used experimentally. Systems based on the acrylate resin Viacryl SM564 + Desmodur N75 (an isocyanate) were developed and tested during the 1970s (Bettembourg 1976; Newton and Seddon 1999), but these particular resins were shown to be unsuitable for the situations in which they were used and are no longer employed in stained glass conservation. However, these kinds of polymer remain potentially useful materials for the protective coating of glass (Newton 1987). Recent research on consolidation of stained glass has also shown that two-part acrylate-isocyanate systems (Desmophen A160–Desmodur N75) perform very well in terms of adhesion, optical stability, and durability when compared to other materials, including methacrylates (J�gers et al. 2000). These systems are, however, irreversible. Limited application has also been found for ethyl silicates, which are theoretically interesting as they enrich the glass with silica, but are also irreversible (Fontaine 1999).
2.2 PARALOID (ACRYLOID) RESINS
There are several types of Paraloid available, including B-44, B-66, B-67, and B-72. They are all thermoplastic acrylic resins available as solution grade or as solid grade acrylic resin (Table 1).
2.2.1 Paraloid B-44
Paraloid B-44 is used in conservation and is slightly harder than B-67. It has a Tg of 60�C and is a methyl methacrylate copolymer (MMA). The manufacturers say that in its solute form, Paraloid B-44 is often blended with other Paraloid resins to adjust those resins to the balance of properties required for a particular application.
2.2.2 Paraloid B-66
Paraloid B-66 is a general-purpose resin with very fast solvent release. It is somewhat softer than B-44 but harder than B-72.
2.2.3 Paraloid B-67
Paraloid B-67 is the most water-resistant of Paraloid resins. It provides a coating that is hard and fast drying and imparts good gloss and color retention. It has a Tg of 50�C and is an i-butyl methacrylate polymer (IBMA). It has been used as a picture varnish and is soluble in less polar solvents2 (such as white spirit) than B-72.
2.2.4 Paraloid B-72
Paraloid B-72 is a copolymer of ethyl methacrylate and methyl acrylate (70: 30) manufactured by Rohm and Haas. Paraloid B-72 is a very stable resin with a Tg of 40�C and a refractive index3 of 1.49.
The popularity of Paraloid B-72 owes as much to its versatility as to its apparent stability. It is sold either in solution or in solid pellet form. The pellets can be dissolved with a compatible solvent to the desired concentration, so that the conservator can vary the viscosity of the resin to suit the application.
As mentioned above, Paraloid B-72 is an ethyl methacrylate: methyl acrylate P(EMA-MA) with a molar ratio of 70: 30. Some concern was expressed about the use of Paraloid B-72 in conservation after the manufacturer changed its composition in 1978. The resin originally had a molar ratio of 68: 32 ethyl methacrylate: methyl acrylate P(EMA-MA) with a lower molecular weight and was soluble in slightly less polar solvents. De Witte and coworkers (1978) carried out a variety of tests to confirm the difference in chemical makeup and concluded that the change would probably not affect the stability of the resin but that long-term aging tests should be considered.
2.3 LIMITATIONS OF PARALOID RESINS FOR STAINED GLASS CONSOLIDATION
The inherently weak chemical bond between the organic consolidants generally used in conservation and the inorganic and weathered gel layer has been
Table .
Types of Paraloid Available as Solution-Grade or Solid-Grade Acrylic Resin
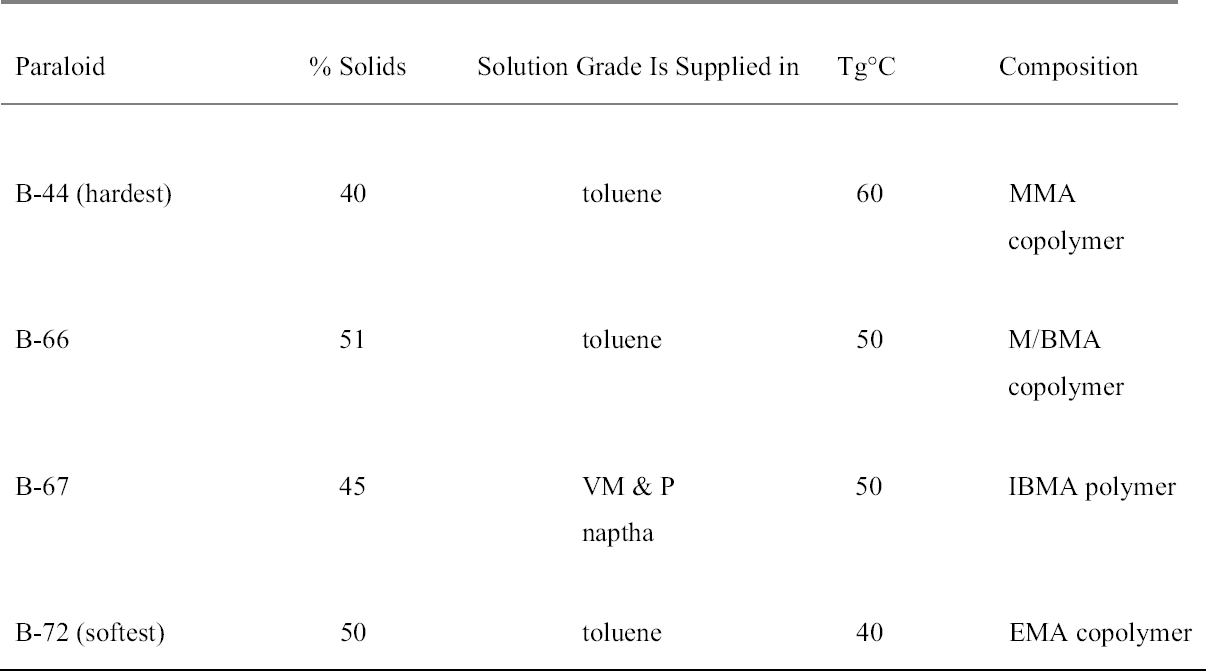 |
remarked upon by numerous authors (Errett et al. 1984; Weintraub and Greenland 1984; M�ller 1996). This limitation applies to all synthetic and natural polymer resins. It is one of the particular difficulties involved in finding effective systems for the consolidation of unstable glass paint.
The chief limitation in terms of durability of acrylic resins such as Paraloid B-72, on the other hand, has to do with their poor water resistance and the problem of permeability in plastics. The degree to which Paraloid resins are susceptible to these phenomena depends to some extent on the form and concentration in which the resin is applied.
Accordingly, authors have been rightly circumspect about the wisdom of using acrylic resins in situations of unbuffered exposure to weathering agents (Sloan 1995). But these limitations have not inhibited the widespread use of Paraloid B-72 in cases in which objects or treated surfaces are not subject to high humidities (and to a lesser extent temperatures). In the case of ancient stained glass in an architectural setting, it is common practice to install protective glazing. Removal of the impact of exterior weathering factors and stabilization of internal temperature and humidity conditions can create an environment that is better suited to preventive conservation of glass paint. Where protective glazing is to be installed, tests and field studies have reported on the suitability of Paraloid B-72 in toluene or another solvent for the consolidation of glass paint and grisaille (Tr�mpler et al. 1996). Nonetheless, accurate microclimatic evaluations are required to assess the likely impact of temperature and humidity ranges on proposed conservation-restoration products, and the properties of a given resin formula must be known.
The question of permeability concerns the risk of water vapor's penetrating a resin film, where over time salts or pollutant compounds trapped beneath may attack the glass substrate. The difficulties involved in creating an effective moisture barrier in the surface treatment of ancient glass using organic resin coatings have been appreciated for many years (Newton 1974; Moncrieff 1975). Both resin concentration and solvent type can significantly influence the properties of a resin film in terms of vapor permeability, photochemical stability, and water resistance.
Additional practical limitations, also concerning resin concentration and solvent type, do give cause for concern in the context of architectural stained glass. By mixing Paraloid B-72 with a solvent at concentrations typically between 2.5% and 7.5%, a low-viscosity material capable of penetrating corroded glass surfaces can be manufactured easily. An experienced conservator can modify the characteristics of the resin to ensure the best result: too low a concentration, and the resin lacks adhesive strength and can be difficult to control; too high, and penetration of the porous glass matrix may be inadequate, while darkening of the surface may be more pronounced.
The solvents most commonly used in association with Paraloid B-72 are acetone, toluene, xylene, ethyl acetate, and diacetone alcohol. The correct choice of solvent and the solvent-solid ratio are important factors in obtaining a resin with suitable workability and flow characteristics. For stained glass this choice must be based, among other things, on the type and condition of the glass paint. For Paraloid B-72 as an adhesive, Koob (1986) has outlined the advantages of acetone, which in addition to being less toxic than some of the others, is released more quickly. Acetone has often been selected as the solvent in the case of stained glass treatments (Learner and Bettembourg 1991), although for consolidation of corroded pigment layers or poorly fired glass paint, some conservators have found that acetone evaporates too quickly. Penetration capacity is reduced, and the ratio of solvent to resin is more difficult to control (Strobl 1999).4 Hence the less volatile solvents have been considered more suitable for use as a consolidant for stained glass, toluene often giving good results. The experience of Tr�mpler and coauthors (1996) indicates that where a grisaille surface is relatively porous, use of toluene has the advantage of securing loose particles relatively quickly and permitting the removal of excess resin before curing takes place. Similarly, Mueller-Weinitschke (1996) reports on the superior properties of toluene over the more volatile alternatives.
Health and safety risks of some of these solvents are well understood. But the handling and application difficulties that these authors comment on may have a direct impact on the effectiveness of the resin consolidant. Most important, because Paraloid resins cure by solvent evaporation, reliable consolidation depends on the ability of the resin solution to penetrate the weakened glass matrix effectively before the resin cures. De Henau (1996) has noted that where Paraloid B-72 is used with a pure solvent, the evaporation rates of the solvent may be too high to ensure adequate consolidation in the depth of a porous body. The faster the solvent evaporates, the more rapidly its viscosity increases and the greater the risk of inadequate penetration of the resin through the porous material.
Choosing the solvent most suited to the particular case in question is thus no less important than the choice of resin. Even the use of a slower-evaporating solvent is not without potential risks. Slow solvent release can mean longer setting times and solvent retention after the initial cure. For refixing of enamel, De Henau (1996) has carried out controlled tests using 10% B-72 in p-xylene and demonstrated how such shortcomings manifest themselves where the evaporation surface of the consolidant is small in relation to the volume of resin applied.
For some types of loose or corroded glass paint, repeated application of the consolidant is sometimes necessary. Some authors have considered that for badly corroded and granular glass paint with very poor cohesive strength, the use of acrylics such as Paraloid B-72 is inappropriate. The increase in gloss and darkening of the surface resulting from the multiple applications needed to secure areas of severe decay are unacceptable (Weintraub and Greenland 1984). Using simulated grisaille panels, Mueller-Weinitschke (1996) has demonstrated the effect, showing that multiple applications of Paraloid B-72 in toluene at 5–7.5% are needed in order to adequately secure the less well-fired areas of grisaille. The degree of darkening is a function of the percentage concentration of resin and the number of applications required.
The light-and heat-aging properties of acrylates have been extensively studied, especially in relation to their use as stone consolidants and coatings (Horie 1987). The effects of artificial light-aging appear to have the most impact in terms of water resistance, though the degree of degradation of the film depends on the substrate type, degree, and conditions of exposure, type of solvent, and concentration of resin. Moderate UV exposure is believed to have low impact on acrylic resins, but higher levels of radiation—such as those encountered in a stained glass panel in situ—may indeed give cause for concern over time.
It is clear, therefore, that the very adaptability of Paraloid resins imposes a greater need for careful scrutiny of the variation of effects observed in different conditions, and on different substrates, using different resin concentrations, solvent types, and methods and numbers of applications.
|