SYNTHETIC FILL MATERIALS FOR SKIN, LEATHER, AND FURS
LINDA NIEUWENHUIZEN
2 APPLICATIONS
2.1 BULKED BEVA 371 FILM
The materials used for this repair are standard for conservation: polyester spun-bonded fabric (i.e., Reemay or Hollytex), BEVA 371 film, glass microspheres, and dry pigments. The only other items needed are a heated spatula, texturing implements, and inpainting materials. BEVA gel (O'Donnell 1996) and BEVA 371 (Kaminitz and Levinson 1988; Jones 1996) have also been used in similar applications. Because of the solvent content in these BEVA formulations, however, and the shrinkage of the fill due to the evaporation of solvent, BEVA 371 film is suggested for use.
2.1.1 Recipe
Ingredients:
- 15.0 � 15.0 cm piece of BEVA 371 film
- (3.5 mil thickness)
- 15 cc 3M K-15 glass microspheres
- dry pigments
For mixing, use a glass or metal container and a heated spatula with a small tip. For the greatest degree of success, a G. Engelbrecht ERSA heated spatula with a small infilling spatula is suggested.
Wearing a particle mask to avoid inhalation of the microspheres, mix the BEVA 371 film and glass microspheres together with the heated spatula. The melting point of BEVA 371 film is 65�C.
Mixing will be somewhat difficult because the BEVA 371 film must melt in order to incorporate the microspheres. Mixing in only 5 cc of microspheres at a time is suggested. After the microspheres are incorporated, add dry pigments to tone the fill material to the appropriate color. Mix the pigments into the BEVA 371 film and microsphere mixture with the heated spatula.
When ready to use, simply scoop the fill material with the heated spatula and apply it to the area of loss. Take care to limit the contact of the heated spatula only to the area of fill material to avoid heat damage to the original skin artifact.
Texture the fill while warm. The fill material cools very quickly and will need to be warmed in the area to be textured in order to properly imprint. Rough sandpaper and stencil brushes may be rubbed onto the surface to mimic suede. A finer sandpaper may be used to achieve a nubuck appearance. Silicone-coated polyester film may be used to smooth a surface. Molds can be taken of adjacent areas; the mold may then be pressed onto the fill surface to achieve the desired texture or pattern (Larsen 1981).
To avoid the problem of dust adhering onto the BEVA 371 fill, it is recommended to use a paint that has a medium with a high glass transition temperature. A glass transition temperature of BEVA 371 film cannot be given (Chludzinski 1997). The fill is easily reversed mechanically,or with heat or petroleum benzine applied sparingly.
Figures 1 and 2 demonstrate the use of the fill material to conserve a damaged skin drum from the Northwest Coast. This drum was manufactured from a deerskin, which upon examination appeared to be minimally prepared by soaking, scraping, and then stretching the skin. In this instance, there were several tears and losses to the skin of the drum that required stabilization and restoration. In order to back the tears, pieces of a feathered-edged spun bonded polyester fabric were applied to the reverse of the drum with BEVA 371 film and a heated spatula. The spatula was set on approximately 65�C. The fabric acts as a backing to hold the tear in place and make a platform for the fill. The BEVA 371 film-glass microsphere-pigment mixture was then applied to the loss area by scooping the fill material with the infilling spatula tip. The fill was flattened using the heated spatula and silicone-coated polyester film. Light sanding followed to decrease the amount of shine created by the polyester film. The prominent design element on the drum was extended onto the fill with Rowney acrylic emulsion paints.
Fig. 1.
Northwest Coast drum before treatment
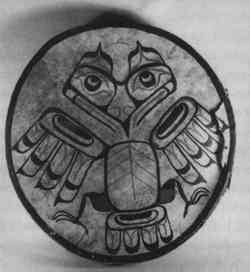 |
Fig. 2.
Detail of the tear after treatment
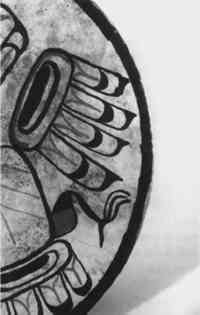 |
In a similar treatment, this fill mixture was used in the restoration of a monitor lizard that was part of a larger Mario Merz installation, Untitled, 1989. The lizard had been dried, stuffed with sawdust, and mounted by inserting a metal armature. A tear at the abdomen-tail junction had been created as a result of the strain placed in this area by the weight of the tail while it was on exhibit in a vertical position. In this application, a backing of spun-bounded polyester was adhered to the underside of the tear with BEVA 371 film and the aid of a tacking iron. The fill material was then applied on top of the spun-bounded polyester platform. The BEVA 371 film-glass microsphere-pigment mixture was placed in the area of loss. A mold was taken of the surrounding skin pattern and used to impart texture to the fill. The fill was made warm with the tacking iron and the mold pressed with gentle pressure onto the fill material to receive the texture. The fill was painted with Winsor & Newton gouache colors and glazed with Paraloid B-72 and dry pigments. In addition, it was necessary to have a mount fabricated to reduce the strain on the lizard abdomen-tail junction. This mount braced the tail and was affixed to the wall for the installation. Figures 3–5 show the BEVA fill application.
Fig. 3.
Monitor lizard before treatment
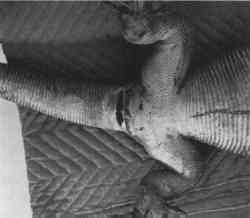 |
Fig. 4.
Deatil of a tear before treatment
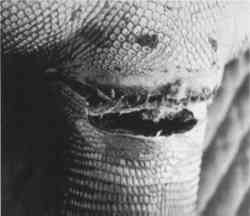 |
Fig. 5.
Detail of the tear after treatment
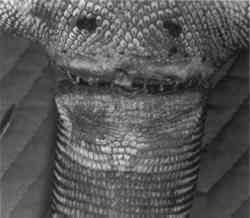 |
2.2 BULKED ACRYLOID F-10
This treatment is a variation on the use of a bulked resin to form a flexible fill. In this example, Acryloid F-10 is mixed with glass microspheres to form a paste that can be applied to a loss directly or used as a formed film made by applying the paste to a mold. Acryloid F-10 is a homopolymer of butyl methacrylate with a low glass transition temperature of 20�C. When the glass microspheres are added to the solvated resin and the solvent is allowed to evaporate, the rheological properties of the resin change greatly to a rather static yet flexible material. To the author's knowledge, the fill material does not exhibit cold flow in controlled museum climates.
2.2.1 Recipe
Ingredients:
- 25 ml Acryloid F-10 (butyl methacrylate supplied in 40% solids in petroleum benzine—Amsco F 9:1). Amsco F is characterized as a C-8 aromatic with a flash point of 150�F. (Wolthman 1996).
- 50 cc 3M K-15 glass microspheres
- For mixing, use a glass or metal container and a spatula.
While wearing a particle mask to avoid inhalation of the microspheres, mix the Acryloid F-10 and glass microspheres together. The recipe will make a material the consistency of marshmallow creme. This recipe yields a fill of approximately 10.0 � 10.0 cm and 0.2–0.3 cm in depth.
When ready to use, scoop the fill material with a spatula and apply it to the area of loss. Though it will still be sticky, the fill can be textured while solvated. Texturing can also be accomplished with the addition of solvents or with a hot spatula after solvent evaporation, utilizing the thermoplastic qualities of the resin. Molds can be taken of similarly textured areas; the fill material can be applied to the mother mold and the solvents allowed to evaporate. At least 48 hours are needed for the solvents to have evaporated enough that the film remains cohesive. Solvents will continue to evaporate after that time, leading to some shrinkage; however, the shrinkage is minimal. The fill remains slightly flexible due to the glass transition temperature of the butyl methacrylate. Cut the fill material to the desired shape. Adhere the fill in place with additional resin or heat the edges of the fill slightly with a heated spatula to adhere. Color compensation should be carried out with a medium having a higher glass transition temperature to decrease the chance of dust adhering to the fill material. Acrylic emulsion paints work well. The fill can be removed mechanically or by using either solvent or heat.
Figure 6 demonstrates the use of this adhesive and microsphere paste to replicate a taxidermy mount of black rhinoceros skin. The black rhinoceros mount is an alum-tanned skin and has been mounted to a prefabricated polyurethane form. A mold was taken of rhinoceros skin, and the paste was applied to the mold. Forty-eight hours were allowed to lapse before removing the fill material from the mold. The fill was then painted with Rowney acrylic emulsion paints. This fill material can be easily cut to shape and adhered with a variety of adhesives, by solvent reforming on the edges to adhere, or with heat.
Fig. 6.
Fig. 6. Replicate cast of Acryloid F-10 and glass microspheres on top of original black rhinoceros skin
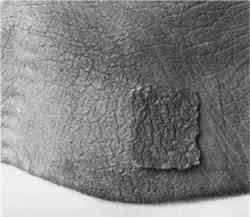 |
2.3 SYNTHETIC FURS
For fur or hair inserts, National Fiber Technologies, Ltd., supplies a broad assortment of synthetic fur fabrics either from their vast stock or to order. The most versatile synthetic fur is an instock white fur made from 18 denier nylon with a four-way spandex stretch backing. There are three standard fur lengths: short (2.5–5.0 cm); medium (8.0–10.0 cm); and long (10.0–15.0 cm). According to the mill where the fabric is woven, the fur can be easily colored with markers, pens, paints, or dyes before utilizing as a fill.1
An alum-tanned and mounted Western Kob (Kobus Kob) from Central Africa was fire- and soot-damaged; the fire and subsequent water damage resulted in gelatinization and shrinkage of the skin, creating a loss on the proper right shoulder. A National Fiber Technologies, Ltd., synthetic fur was utilized to fill and integrate the loss.
First a template was made of the area of loss. This template was transferred to the synthetic fur, and a fill section was cut. A sharp scalpel was used to cut the nylon fur from the reverse side; care was taken to cut only the stretch backing and not the synthetic hair. The synthetic fur fill was trimmed and layered to match the hairs of the original fur. The synthetic fur was inserted into place using Acryloid F-10 in acetone: the adhesive was applied directly to the substrate (a prefabricated polyurethane Western Kob mount) by placing the edges of the fur fill directly to the adjacent sides of the extant fur and skin. The synthetic fur was toned and colored with Magna colors by brush application. Figures 7–9 illustrate this technique.
Fig. 7.
Western Kob before treatment; note damage on lower proper right shoulder
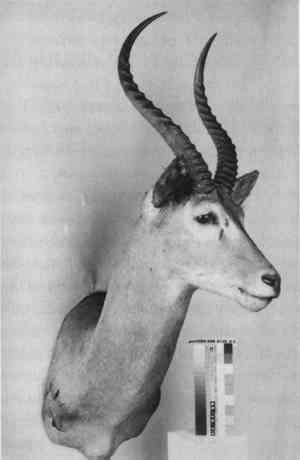 |
Fig. 8.
Detail of fill before toning
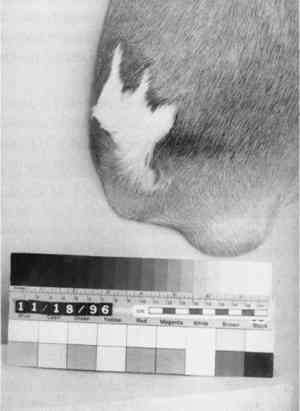 |
Fig. 9.
Detail of the fill after treatment
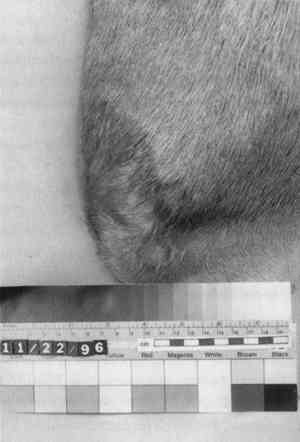 |
|